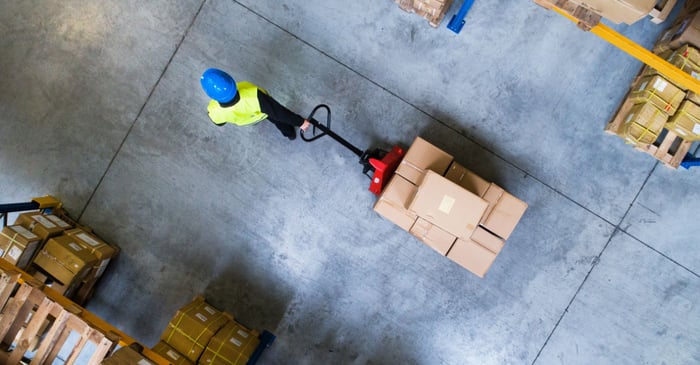
It is no secret that COVID-19 damaged the modern-day supply chain. From silicon shortage to toilet paper stockouts, the marketplace has seen it all. According to a survey from the Institute for Supply Management, 95% of the businesses had to endure operational troubles during the initial pandemic days in April 2020.
While businesses cannot prevent such disruptions, they can prepare themselves to persevere through them.
The Cin7 team has compiled a list of strategies to build a resilient supply chain for your business and help gain an edge over the competition.
What is supply chain resilience?
The origins of the supply chain resilience concept can be traced back to the work of C.S. Holling, an ecologist who coined the term “ecological resilience.” It refers to the ability of an ecosystem to maintain normal patterns despite being subjected to the damage arising from ecological disruptions.
Supply chain resilience is defined as an organization’s ability to recover from unexpected supply chain disruptions using its “ecosystem’s” existing capabilities, ensuring that the operations run smoothly and the customers remain satisfied.
Challenges and risks in building successful supply chains
The pandemic disrupted nearly every stage of an organization’s supply chain. The effect was global and prolonged.
As bad as the pandemic was and continues to be, it is just one of the many factors that disrupt the smooth functioning of the supply chain. Here are some scenarios that pose risks to the supply chain:
#1 Operational risks
Operational risks occur because of breakdowns in normal working operations. Both technical and non-technical reasons can pose this risk.
Example: Machine failure due to poor maintenance (technical) and mismanagement (non-technical). This risk can be classified as internal risk, i.e., it can be fully controlled and avoided by the organization.
#2 Financial risks
Delays from the supplier can cause delays in your production process. This type of risk emerges due to shortcomings in the suppliers’ finances and revenue.
Example: The supplier reduces the production of your raw materials due to their own financial woes or files for bankruptcy. To combat such a scenario, either extend them a line of credit or search for an alternative supplier.
#3 Legal risks
Legal risks arise when organizations are slapped with lawsuits, whether they are frivolous or not. Fighting lawsuits takes a toll on your time, money, and resources. Severe cases can also tarnish your reputation, leading to a loss in revenue and business development.
Example: If a lawsuit for an intellectual property violation is filed against your company or you are fined for breaking environmental laws, any suppliers who get trapped in either scenario can catastrophically disrupt the supply chain of your business.
#4 Geopolitical risks
Globalization has converted the entire world into a connected village, where consumers are no longer dependent on geographical boundaries to purchase items.
Producers benefit from globalization, as they are no longer restricted to sourcing their raw materials from the same region. Faster connectivity ensures that they can order from any corner of the world at a price that fits their budget.
Global connectivity also comes with its challenges. While businesses operate under the trade and commerce laws of their nation, working with partners from various countries adds various layers of complexity.
Situations like political turbulence, governmental policy changes, and war outbreaks can hinder your suppliers’ capacity to make timely delivery.
Example: The US-China trade war and Brexit are classic examples of geopolitical risks.
#5 Natural disasters
Hurricanes, earthquakes, and other natural disasters have been disrupting the supply chain for ages. Such disasters can be classified as external risks, as they are not in the control of the business. Regardless of the classification of risk, these calamities lead to port closures and cargo flight cancellations, in addition to creating capacity constraints and supply shortages.
Even climate change affects the operations of businesses. Research from the
United Nations Development Program (UNDP) suggests that rising temperatures could lead to adverse effects on the workers.
According to the UNDP, climate change’s economic impact on labor productivity could reach $2.5 trillion in global losses by 2030.
Example: In 2017, Hurricane Harvey and Irma—fueled by symptoms of climate change—hit the gulf coast in a span of two weeks. These hurricanes left a trail of physical and economic destruction, including a severe disruption to the regional supply chain.
#6 Cyberattacks
The rise of digitalization has also given rise to cyber security attacks. In fact, cyberattacks have become a leading cause of supply chain vulnerability.
The supply chain becomes a tempting target for hackers as vendors often possess sensitive data about companies or have enough access to allow for privilege escalation.
As attacks of such nature become more common, manufacturers must invest in cybersecurity proactively. This is for safeguarding them as well as their clientele’s data.
Example: Airbus is one of the world’s largest airline manufacturers, and they were subjected to a series of cyberattacks in 2018. The hackers gained access to the confidential documents containing the schematics for classified military transport planes through the attack.
Strategies to build a resilient supply chain
A robust supply chain resilience strategy requires two complementary supply chain pillars: resistance and recovery capacity.
Resistance capacity is the ability of a supply chain system to minimize the overall impact caused by disruption. It can be done in two ways:
- Evasion: Entirely avoiding the factor causing disruption in the supply chain.
- Containment: Minimizing the period between an event and the time when the supply chain starts to recover from the effects.
Recovery capacity is a supply chain’s ability to restore itself to the level prior to its disruption.
For organizations to achieve true supply chain resilience, they need to be prepared to confront obstacles before they cause any considerable damage.
There are seven distinct strategies to build strong resilience and ensure quick recovery.
#1 Creating buffers
Manufacturers should create buffers to build resilience against minor operational risks like employees calling out sick or shop floor machines breaking down. Building buffers and making them a part of your operational process reduces your dependence on the supply chain working at full capacity.
According to one survey, 21% of the supply chain experts consider maintaining buffer stock as a solid indicator of resilience. The challenge of maintaining high buffer stock can increase your carrying costs, so the optimal buffers need to be strategically planned.
#2 Optimized inventory control
If you are relying on a single warehouse for storing your inventory, consider the option to spread your inventory across different locations.
A natural disaster damaging the warehouse or a virus outbreak among warehouse employees would undoubtedly lead to fulfillment delays.
Splitting the inventory helps minimize the risk and helps expand your customer reach by reducing shipping costs and speeding the shipping time.
Another way to build resilience is to invest in technology that provides real-time visibility into your supply chain. It helps monitor your supply chain performance and identify any and all bottlenecks. Inventory management software assists you to make better inventory decisions and set up reorder points to ensure that you never run out of stock.
Investing in an integrated warehouse management system helps you with better inventory management while reducing the number of errors. Successful organizations devise strategies to manage the longer lead times and methods to counter the unexpected surge in demand, while building replenishment models to ensure that the goods are available when needed.
#3 Investing in human resources
Human resources are necessary to complete the work but having experienced supply chain managers with market knowledge helps navigate through unexpected disruptions.
Merely hiring exceptional people is not enough—the business also needs systems built and SOPs to establish production infrastructure. Your team should have personnel dedicated to fostering better supplier relationships and for commodity management.
Commodity managers monitor the market to scout for new products in demand, price changes, and the latest supply chain developments. This information helps ensure staying on top of market trends and aids in better cost management and decision making.
Helpful hint: The pandemic has been a catalyst to the remote working environment. Such work environmental changes affect the wellbeing of the workers, both physically and psychologically.
The mental well-being of the workers must not be overlooked. “Emotional resilience” is every bit as important as supply chain resilience.
#4 Having multiple supply partners
The concept of partnering with multiple suppliers for procurement is referred to as multisourcing.
One piece of famous investment advice is “Don’t put all your eggs in one basket.” Similarly, relying on a single partner for procuring materials is filled with risk, so partnering with multiple vendors will ensure that your proverbial eggs are placed in several baskets.
Multisourcing ensures that your supply chain does not get disrupted when your primary supplier fails to deliver on time, as you can source it from someone else. It also helps with incentivizing competitive pricing among suppliers so that you get the best returns.
The pandemic demonstrated that diversification is an integral part of building supply chain resilience. For example, China is lauded as one of the world’s leading raw materials suppliers but had production grind to a halt due to Covid-19. When the lockdown was imposed in 2020, manufacturers sought and partnered with different countries like Mexico and Vietnam to expand their network.
Helpful hint: While working with multiple suppliers, you should have a dedicated team for supplier relationships. The supplier relationship manager focuses on developing deeper relationships with suppliers by understanding their core strategies and approaching them with mutually beneficial opportunities. If the supplier is working on limited capacity, there is a good chance they will prioritize the business that has built better relations with them.
#5 Effective communication
Managing supply chains requires a cross-functional effort from all the departments. Businesses need to be agile and loosen the silo structure, which inhibits the flow of information.
As the trend for hybrid working increases, companies should allocate the necessary IT resources for smooth operations and orient them with the relevant tools for communication. Managing virtual teams is very different from conventional teams, so provide managers adequate training to lead them.
Helpful hint: Keep your employees and suppliers in the loop during any periods of disruption. Provide them with relevant company information to help them make informed decisions and minimize errors.
#6 Planning and forecasting
When introducing a new product to the marketplace, it takes approximately two to three years for product development, and the lead time takes approximately 25 to 40 weeks.
It means that to deliver a product during the holidays, a business must start the plan in March. However, businesses forecast demands using their historical data, yet no demand forecasting plan would have predicted that a pandemic would be declared in March, leading to lockdowns and drastically changing customer preferences.
A feasible way to combat such forecasting issues is to invest heavily in analytics and upgrade supply chain technology. A business continuity plan identifies all the potential risks, quantifies them, and then devises a plan to deal with them, while keeping the organization running concurrently.
#7 Developing ecosystem partnerships
Many eCommerce businesses lack the supply chain infrastructure to manage the inbound and outbound logistics. This is where third-party logistics (3PLs) come to the rescue.
Partnering with 3PLs can offer reduced costs, a warehousing facility, and access to a better transportation network. This can help streamline the fulfillment process and diversify the fulfillment process so that manufacturers can prioritize their core competence.
Third-party logistics partners also bring their years of experience to the table, helping you optimize your solid supply chain infrastructure and build resilience.
Measuring supply chain resilience
To test the efficacy of your planning, McKinsey recommends a stress test model. This model quantifies the supply chain resilience against five factors:
- Industry attractiveness
- Customer exposure
- Operations exposure
- Corporate resilience
- Supply chain exposure
Apart from the stress test model, there are three core metrics that help in evaluating supply chain resilience.
#1 Time to survive
This metric refers to the time to resume business operations after a disruption.
For instance, the time to survive metric for some factories in China was nearly three weeks. It reflects how long it takes to establish the necessary safety measures (like offering personal protective equipment kits) and obtain clearance from the government.
In this phase, the companies need to answer some key questions around:
- Compensating the people
- Bringing people back to the workplace
- Taking corrective measures to reopen their premises
In a nutshell, time to survive answers the question, “How long does it take to reopen the business?”
#2 Time to recover
Recovery time is how long it takes to return your business to the capacity it had before the disruption.
Even though the Chinese factories started to function again after the Covid-19 outbreak, they were only running at a fraction of their standard capacity. This occurred due to a lack of workers and loss of production time. It took an additional three to four months to recover.
Prepare and protect your business by examining how long it would take to get operations back in working order.
#3 Time to thrive
The time to thrive arrives after the recovery phase, but only after an evaluation of how the business confronted the crisis.
It juxtaposes the state of business before and after the crisis and determines if and how the company learned any lessons from the disruption and improved.
Regardless of what analysis emerges during this phase, businesses should be ready to pivot their offerings to match what the market demands now. For instance, many restaurants now offer home delivery or pick-up due to the consumers’ behavioral change caused by the lockdown.
Once a company determines how it has or hasn’t improved after facing the crisis, the time to thrive is not far off.
In summary
Businesses need to be agile and flexible enough to adapt to the changes caused by disruptions.
Building a resilient supply chain mitigates the risk and boosts operational efficiency. Companies that invest in supply chain resilience often see shorter product development cycles than those that overlook it, which can be a competitive advantage.
By partnering with Cin7, you can automate your workflow as well as get better analytics and insights about your inventory, which helps in data-driven decision making. You can also partner with the best 3PLs through our integrations.
The experts at Cin7 can help you build a resilient supply chain for your business. Book a call now to discover more!
More from the blog
View All Posts
Why your business should use supply chain visibility
Read More
12 reasons using Cin7 for your Amazon business is beneficial
Read More