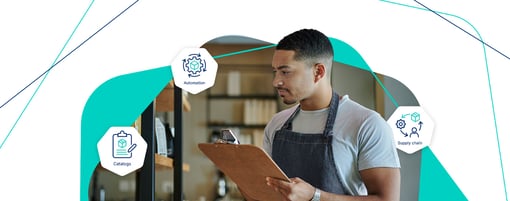
In 2013, Walmart experienced an inventory crisis, losing over $3 billion due to out-of-stock merchandise and a lopsided inventory turnover ratio.
Sure, plenty of mammoth companies have mismanaged their inventories and lost billions while remaining successful. However, with only half of small businesses in the U.S. making it to year five, prioritizing effective small business inventory management at the SMB level is a critical means of growth and survival.
Inventory management techniques provide cost-saving and profit-boosting benefits for small businesses that help them remain profitable and competitive. Below is a list of some of the most popular and effective inventory management techniques and directions for using them to improve your business.
Jump to:
- Economic order quantity (EOQ)
- Minimum order quantity
- ABC analysis
- Just in time inventory management
- Safety stock
- FIFO & LIFO
- Reorder point formula
- Batch tracking
- Consignment inventory
- Perpetual inventory management
- Dropshipping
- Lean manufacturing system
- Sigma
- Lean Six Sigma
- Days sales of inventory (DSI)
- Cross docking
- Materials requirement planning (MRP)
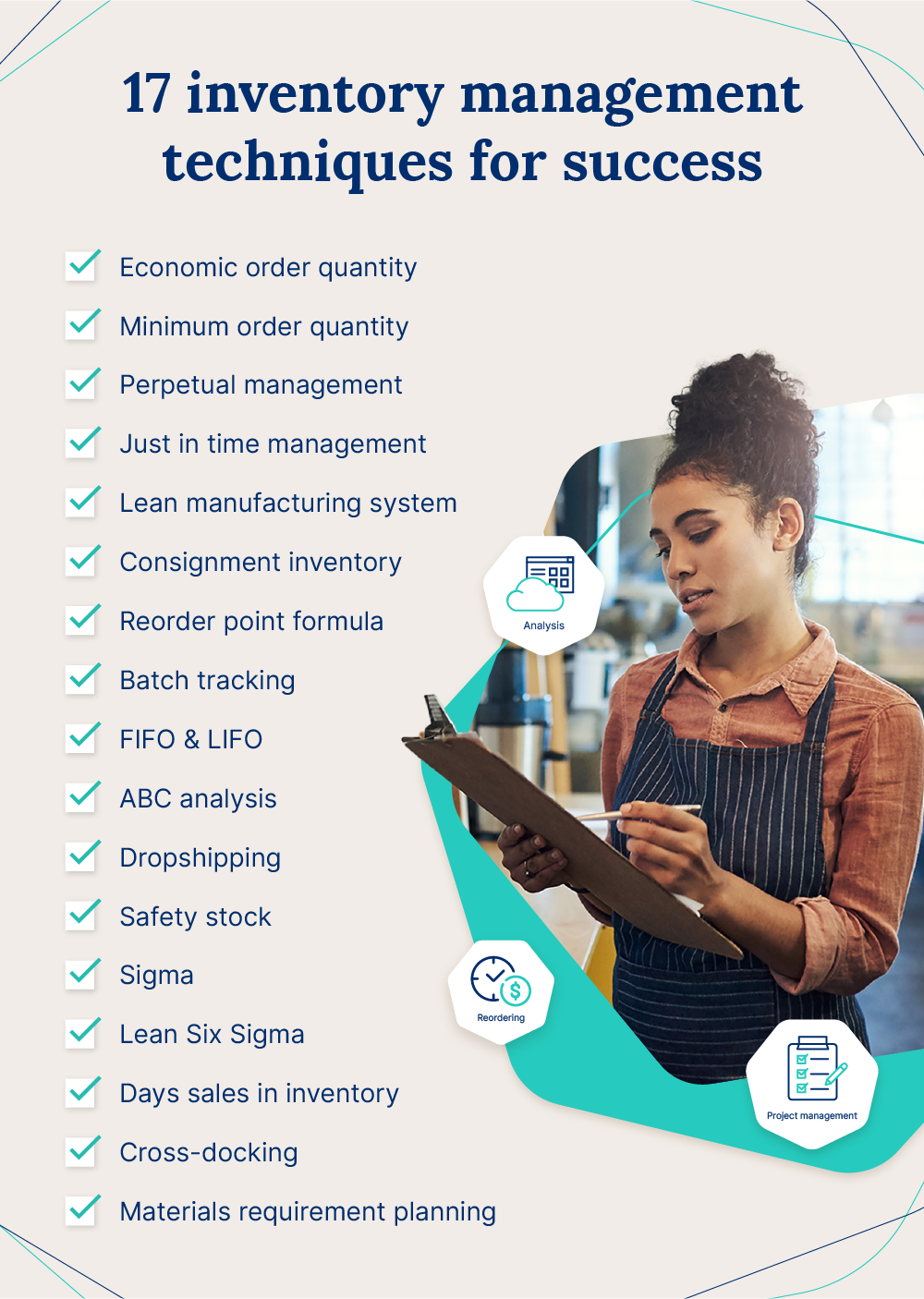
1. Economic order quantity (EOQ)
Economic order quantity (EOQ) is a method that uses the lowest amount of inventory necessary to meet peak customer demand without going out of stock or producing obsolete inventory. It’s used to create inventory control, or to minimize costs while maximizing profits through inventory management.
EOQ uses three variables in its formula:
- Demand: The units needed for a product for a specific period
- Relevant ordering cost: The ordering cost per purchase order
- Relevant carrying cost: The carrying costs for one unit, assuming the unit is in stock for the period used for demand
The formula for calculating EOQ is:
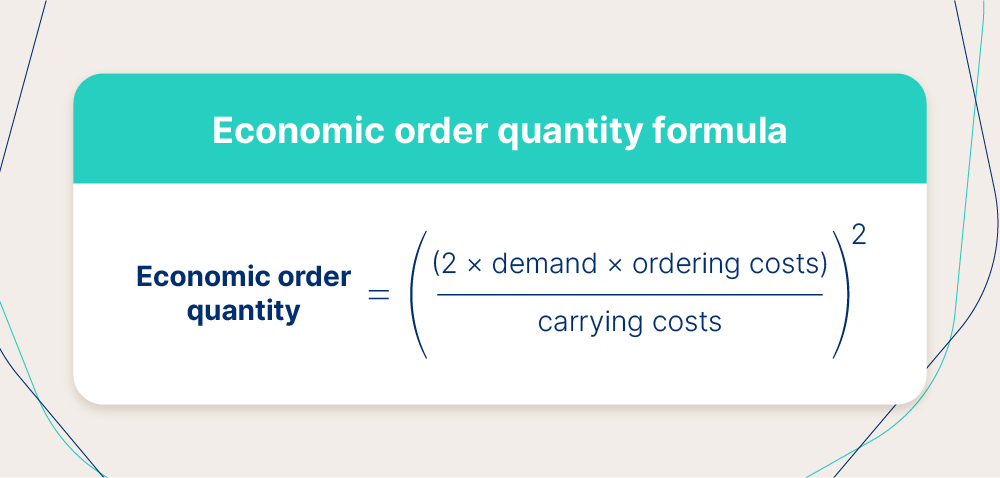
Economic order quantity = square root of [(2 x demand x ordering costs) ÷ carrying costs]
Best for: Quickly growing businesses with regular inventory needs
Benefits:
- Minimizes holding costs
- Provides accurate costing
Considerations:
- Lower periods of demand may leave you with excess inventory
2. Minimum order quantity
Minimum order quantity (MOQ) refers to the lowest amount of stock that a supplier will sell to you. If you don’t buy the MOQ, the supplier won’t sell you the product.
For retailers, MOQs are especially helpful in limiting excess stock and maintaining steady profit margins. By only offering products in bulk, retailers can more easily balance production and demand.
Best for: Retailers and wholesalers looking to balance production costs with demand
Benefits:
- Limits excess stock
- Helps companies maintain a steady cash flow
Considerations:
- May deter customers unwilling to buy in bulk
3. ABC analysis
ABC analysis is an inventory management technique that involves sorting inventory into three categories, according to how well they sell and how much they cost to hold:
- A items: Best-selling items that are cheap to hold and don’t take up warehouse space
- B items: Middle-tier items that sell regularly but may cost more than A-items to hold
- C items: Inventory that makes most of your inventory costs, but doesn’t drive much profit
ABC analysis helps you make smarter decisions about reordering, which, in the long run, can reduce obsolete inventory and help optimize your inventory turnover ratio.
Best for: Small businesses struggling to manage inventory levels
Benefits:
- Helps make decisions about product prioritization
- Beneficial for setting accurate reorder points
Considerations:
- Doesn’t account for seasonal demand
4. Just in time inventory management
Just in time inventory management (JIT) is the process of making:
- Only the necessary products
- Only the necessary amount of products
- Only when the necessary products are needed
Essentially, JIT creates goods to order. When orders come through, manufacturers only order the inventory needed to produce those specific items.
The JIT system can be integral in minimizing costs, excess inventory, and unnecessary warehousing. However, keeping up as order volume grows can be very difficult.
Best for: Growing companies looking to reduce costs as much as possible
Benefits:
- Minimizes holding costs
- Reduces excess inventory and waste
Considerations:
- Difficult to sustain once sales volume grows
5. Safety stock
Safety stock inventory is a small surplus inventory that companies keep on hand to guard against variability in market demand and lead times. Safety stock plays an integral role in the smooth operations of your supply chain in various ways, such as:
- Protecting against unexpected spikes in demand
- Preventing stockouts
- Compensating for inaccurate market forecasts
- Buffering against longer-than-expected lead times
Without safety stock inventory, you risk:
- Loss of revenue
- Lost customers
- Market share loss
The safety stock formula is relatively straightforward and requires only a few inputs for calculation. The formula for finding safety stock is:
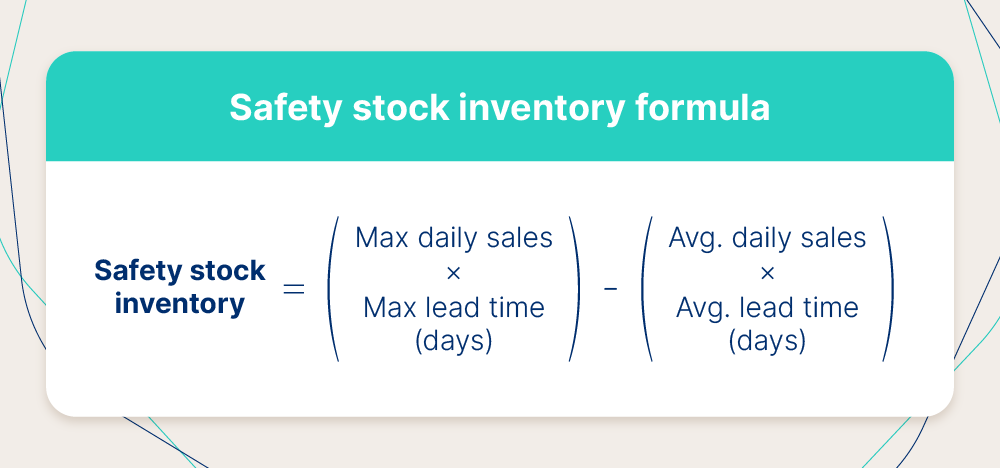
(Max Daily Sales x Max Lead Time in Days) – (Average Daily Sales x Average Lead Time in Days) = Safety Stock Inventory
Best for: Companies in industries that experience regular demand fluctuation
Benefits:
- Protection against unexpected demand spikes, increased lead times, or inaccurate forecasting
Considerations:
- Risk losing money to excess inventory
6. FIFO & LIFO
FIFO and LIFO are two widely used accounting methods in inventory management that can determine accurate cost and profitability.
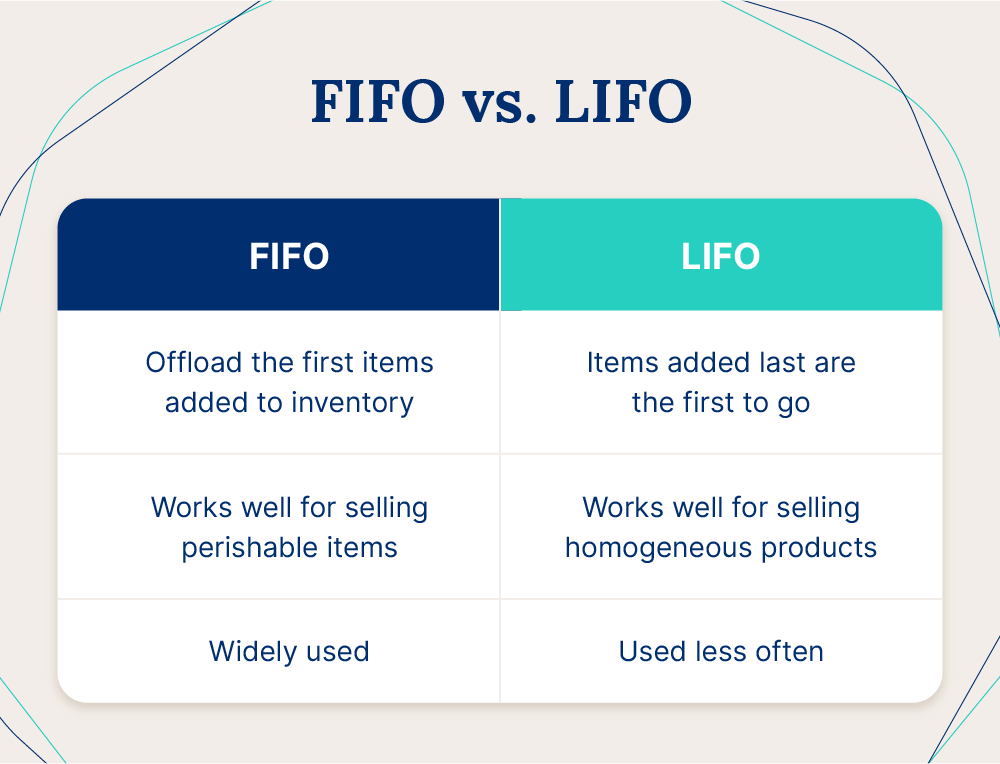
FIFO (first-in-first-out) is an inventory accounting method based on the idea that the first items in your inventory should be the first to leave. LIFO (last-in-first-out) conversely states that the last items in your inventory should be the first ones that leave.
Food and beverage companies use FIFO since they deal with perishable goods. LIFO is a great method for non-perishable homogeneous goods like raw materials.
Best for: Food and beverage companies (FIFO) and raw materials (LIFO)
Benefits:
- Both methods provide accurate costing so you can better value your inventory
Considerations:
- In FIFO, costing can become less accurate in periods of high inflation
7. Reorder point formula
The reorder point formula tells you approximately when you should order more stock, or the lowest amount of inventory you can sustain. Businesses can take the guesswork out of reordering by determining reorder points, so they never have too little or too much.
The formula for finding the reorder point is:
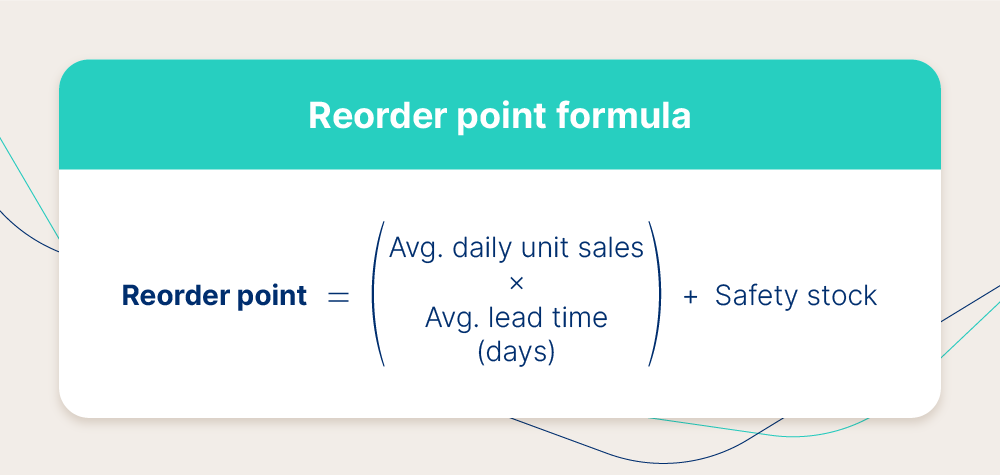
(Average Daily Unit Sales x Average Lead Time in Days) + Safety Stock = Reorder Point
It can be monotonous manually setting reorder points, so getting them correct is pivotal so you don’t experience stockouts. The best inventory management software uses automation to determine your reorder point for you so you never fall victim to unexpected disruptions.
See what automated inventory management can do for you.
Best for: Industries with little to no demand fluctuations
Benefits:
- Avoid stockouts and excess inventory
Considerations:
- Unexpected demand shifts can cause reorder points to change
8. Batch tracking
Batch tracking is a process that uses batch numbers to trace goods along the distribution chain using batch numbers.
Through batch tracking, you can keep tabs on all your raw materials, WIP inventory, and finished goods — ensuring you don’t fill your warehouse with unusable items.
Best for: Food and beverage companies that need to track expiration dates
Benefits:
- Fast recalls
- Streamlined tracking
- Improved relationships with suppliers
Considerations:
- Higher volume of WIP inventory
- Higher possibility of employee downtime
9. Consignment inventory
Consignment inventory is a business arrangement where the consignor, usually a vendor or wholesaler, gives their goods to a consignee, which is generally a retailer. In this agreement, however, the consignee doesn’t have to pay for the goods until they sell them.
This inventory management technique allows retailers to enjoy less risk and low ownership costs, which can be great for testing new products on the market.
Best for: Retailers looking for lower carrying costs
Benefits:
- Low cost of ownership
- Less risk for retailers
Considerations:
- Low demand for consignor products
- Risk of holding unsold products from the consignor
10. Perpetual inventory management
A perpetual inventory management system, also known as a continuous inventory system, prioritizes real-time inventory tracking so no transaction goes unaccounted for.
With real-time updates, businesses can more accurately forecast demand and be more proactive about reorders and inventory turnover.
Best for: Multi-location retailers who experience seasonal demand
Benefits:
- Simplifies multi-location inventory management
- Improves forecasting
- Helps optimize inventory turnover ratio
Considerations:
- More expensive to implement
- Can have compounding problems for a company if tracking is inaccurate
11. Dropshipping
Dropshipping is a business model that allows you to sell and ship products you don’t own and don’t stock. Your suppliers –– wholesalers or manufacturers –– produce the goods, warehouse them, and ship them to your customers for you.
The dropshipping process is relatively simple:
- Receive an order
- Forward the order to your supplier
- Supplier fulfills your order
Dropshipping allows individual product sellors the luxury of low costs to get started and low inventory costs.
Best for: Those looking to sell products as a side hustle
Benefits:
- Low startup costs
- Low order fulfillment costs
- Test products with little to no risk
Considerations:
- Difficult to build a brand
- Low-profit margins
- Competitive market
- No supply chain control
12. Lean manufacturing system
Lean manufacturing, often referred to as lean warehousing, is a system for maximizing value for the customer while minimizing manufacturing waste.
This system seeks to prevent three types of waste:
- Muda: Parts of the manufacturing process that create waste
- Mura: Processes that don’t drive value to the customer
- Muri: Tasks detrimental to employee well-being
The five principles of a lean manufacturing system are:
- Value: A company delivers the most valuable product to the customer.
- Value Stream: Map the steps and processes required to manufacture those valuable products.
- Flow: Undergo the process of ensuring all of your value-adding steps flow smoothly without interruptions, delays, or bottlenecks.
- Pull: Products are built on a “just in time” basis so that materials don’t get stockpiled and customers receive their orders within weeks, instead of months.
- Perfection: Make lean thinking and process improvement a core part of your company culture.
By minimizing or eliminating Muda, Mura, and Muri while adhering to the five principles, champions of lean manufacturing believe this inventory management technique can produce the highest-quality products while increasing your revenue and productivity.
Best for: Manufacturers looking to decrease production costs
Benefits:
- Reduces manufacturing waste
- Bolsters efficiency
- Increases quality of products
Considerations:
- Longer onboarding period for staff
- Can be expensive to implement
13. Sigma
Sigma, or Six Sigma, strives to combat waste by producing almost no defective products. The idea behind Sigma is to improve the manufacturing process to reach near perfection.
The first and most-used method in Six Sigma is a 5-step process called DMAIC:
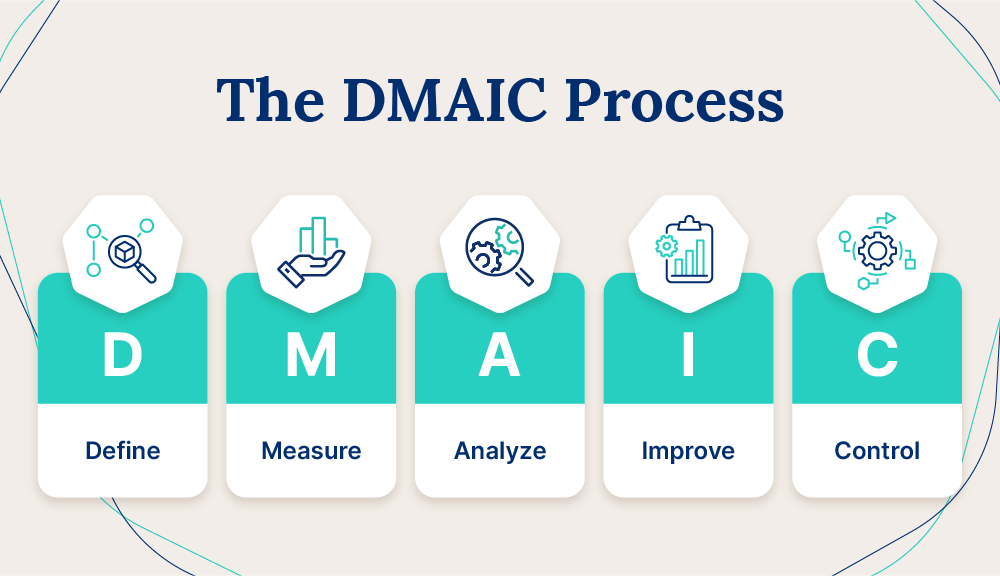
- Define
- Measure
- Analyze
- Improve
- Control
The DMAIC process uses data and measured objectives to create a cycle of continuous improvement in your manufacturing methods.
Best for: Sales teams looking to grow their customer base
Benefits:
- Decreased waste
- Increased productivity
- Applicable to any industry
Considerations:
- Chasing continuous improvement may lead to increased costs and overhead through improvements
14. Lean Six Sigma
Lean Six Sigma combines lean manufacturing with Six Sigma to create a complete system that removes waste and reduces process variation for streamlined manufacturing and optimal product output.
Lean Six Sigma primarily uses Six Sigma’s processes and methods as the backbone of the system –such as DMAIC –– to drive focused manufacturing improvements while incorporating many lean techniques and tools to reduce wasteful steps and processes.
Best for: Industries with more complex processes, like engineering and manufacturing
Benefits:
- Less strict as traditional lean methodology
- Increases productivity and employee satisfaction
Considerations:
- Complex for companies to implement
- Takes a long time to onboard staff
15. Days sales in inventory (DSI)
Days sales in inventory (DSI) measures the time it takes for a retailer to sell its entire inventory. When you determine your company’s DSI, you can quantify if your inventory is flying off the shelves. You’ll also gain other insights, like:
- How effectively you manage inventory
- What demand looks like for your inventory
- How much capital is tied up in inventory
Use the following calculation to find DSI:
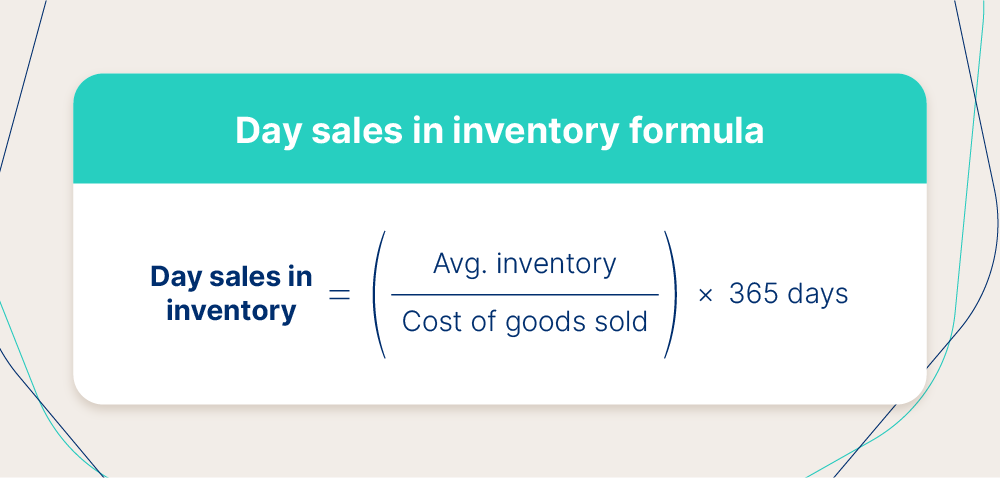
DSI = (Average Inventory / Cost of Goods Sold (COGs)) x 365 days
By learning your DSI, you inherently learn about the liquidity of your inventory, which can help you make smarter decisions about your products.
Best for: Retailers selling physical inventory
Benefits:
- Allows you to make smarter reordering decisions
- Can give you a competitive advantage in your market
Considerations:
- Doesn’t account for changing market conditions
16. Cross-docking
Cross-docking is a supply chain tactic used to reduce inventory costs and speed up delivery times. Essentially, cross-docking removes the storage stage of the product lifecycle. In this method, products move directly from the truck, from the warehouse they were produced into outbound delivery trucks headed to customers’ doors.
Cross-docking plays into the lean methodology. By eliminating any storage phase, companies can delete time that’s not valuable to customers, thus saving inventory costs and increasing efficiency.
Best for: Retailers with high inventory turnover looking to reduce logistics costs
Benefits:
- Reduced transportation and procurement costs
- Quicker delivery times
- Less manual handling of products
Considerations:
- Requires more planning and a strong relationship with your suppliers
17. Materials requirement planning (MRP)
Materials requirement planning (MRP) describes a process where manufacturers use both demand forecasting and the bill of materials (BOM) of a product to accelerate the production process. Manufacturers look specifically at three elements in MRP:
- What they need
- How much they need
- When they need it
By establishing these elements before production, manufacturers can establish a more efficient process that doesn’t create waste.
Best for: Product-based manufacturers struggling to meet inventory requirements
Benefits:
- Prevents excess stock and wait times
- Accounts for possible disruptions to the production process
Considerations:
- Only works if you’ve input the correct information into your BOM
Tips for improving your inventory management process
After identifying the inventory management technique that makes the most sense for your business, you can finetune other processes and fully achieve inventory flow.
Here are a few other best practices that can complement your chosen inventory management technique:
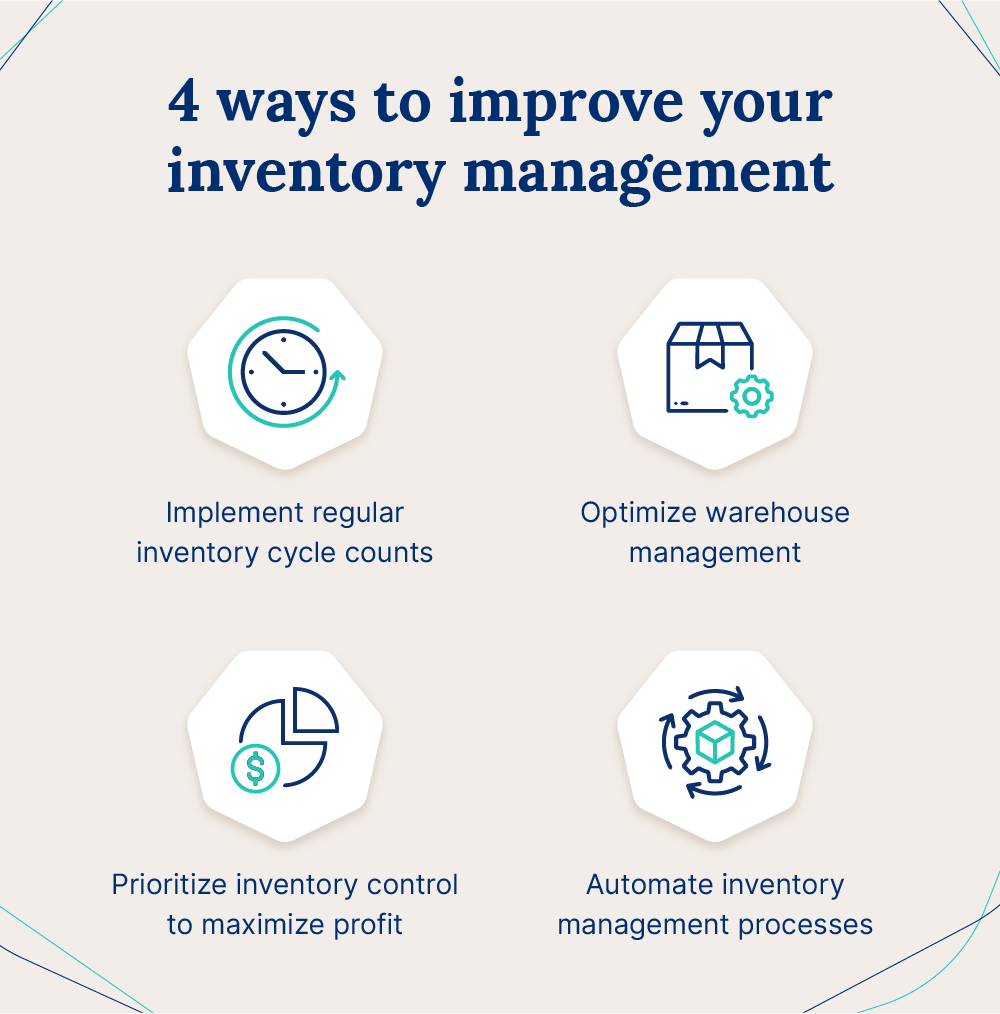
- Implement regular inventory cycle counts: Regular inventory cycle counts work to ensure physical inventory always matches inventory records. Getting in the cadence of regular cycle counts will help avoid any setbacks down the road.
- Optimize warehouse management: Optimizing your warehouse management system is integral to a sound inventory management process. This may mean incorporating lean manufacturing principles, optimizing warehouse design, or identifying inefficiencies in your current warehouse management.
- Prioritize inventory control: Inventory control, or maximizing profit while minimizing cost, should guide your inventory management process.
- Automate inventory management processes: Automated inventory management can help you save money and time while accelerating growth. Automation reduces human errors that can pause momentum and set your growth back.
Industry-Specific Tips and Advanced Strategies for Effective Inventory Management
Industry-Specific Tips
Retail Industry Inventory Management
- Managing Inventory: Utilize an order management system to track inventory data in real-time, reducing stockouts and overstocking.
- Inventory Accuracy: Conduct regular physical inventory counts to ensure accuracy and prevent inventory shrinkage.
- Customer Order Fulfillment: Implement a robust order management system to streamline the process and enhance customer satisfaction.
Manufacturing Industry Inventory Management
- Inventory Forecasting: Use advanced inventory forecasting tools to predict future demand and maintain optimal stock levels.
- Operational Efficiency: Automate inventory movement and handling to increase operational efficiency and reduce holding costs.
- Supply Chain Management: Integrate your inventory management system with supply chain management software for seamless coordination.
Healthcare Industry Inventory Management
- Inventory Accuracy: Ensure precise inventory data management to maintain the availability of critical inventory items.
- Inventory Audit: Conduct frequent inventory audits to ensure compliance with regulatory requirements and maintain inventory accuracy.
- Stock Management: Implement strict stock management practices to reduce waste and ensure the availability of essential medical supplies.
Advanced Inventory Strategies
Just-In-Time (JIT) Inventory management
- Definition and Benefits: JIT involves ordering and receiving inventory items only as needed, minimizing holding costs and reducing waste.
- Implementation Process:
- Develop strong relationships with reliable suppliers.
- Use inventory forecasting to accurately predict demand.
- Implement an efficient order management system to ensure timely deliveries.
Drop Shipping
- Definition and Benefits: Drop shipping allows selling products without holding inventory. Orders are fulfilled directly by suppliers, reducing overhead costs and inventory shrinkage.
- Implementation Process:
- Partner with reputable drop shipping suppliers.
- Integrate your e-commerce platform with supplier systems for seamless order processing.
- Monitor supplier performance to ensure timely delivery and maintain customer satisfaction.
Automated Replenishment
- Definition and Benefits: Automated replenishment systems use real-time inventory data to trigger reorders automatically, ensuring optimal stock levels and reducing the risk of stockouts.
- Implementation Process:
- Implement an inventory management system with automated replenishment capabilities.
- Set reorder points and quantities based on inventory forecasting data.
- Continuously monitor inventory levels and adjust settings as needed to align with future demand.
Start a free trial of Cin7 today.
Frequently asked questions
Still wondering about the best inventory management method for your business? We’ve got you covered. Here are some frequently asked questions and answers about inventory management techniques.
What are the four inventory management techniques?
The four most popular inventory management techniques are:
- FIFO
- Just in time inventory management
- Materials requirement planning
- Economic order quantity
These four methods tend to be the most widely used due to their proven success and their versatility to fit into several different business models.
What is the most commonly used inventory management method?
First-in-first-out (FIFO) is the most commonly used inventory management technique in manufacturing. Manufacturers like using the FIFO method because its structure closely resembles how stock typically moves through the inventory lifecycle.
Which inventory technique is best?
Many believe that FIFO is the best inventory technique because of how closely its model resembles the inventory flow.
In most cases, the first items you add to your inventory will be the cheapest since prices typically rise over time. As a result, those items will be most likely to sell first.
What is the best inventory method for a small business?
FIFO and just in time inventory management are the best inventory methods for small businesses.
While FIFO may provide your small business with the most accurate cost and profitability information, just in time inventory, while risky, can help small businesses save money in their early years.
How do you overcome poor inventory management?
Inefficient inventory management can have compounding effects that can stunt a business’s growth and cause you to spend unnecessary time and money. While these techniques can add efficiency to your inventory processes, software can collect data to make smarter decisions for you, so you can focus on growing your business.
Connecting your inventory management through comprehensive software is a surefire way to achieve flow and add efficiency to your existing processes.
Level up your inventory management techniques with a free trial of Cin7.
More from the blog
View All Posts
The complete guide to medical device inventory management: Best practices and solutions
Read More
Manufacturer Part Number: Benefits and Applications
Read More