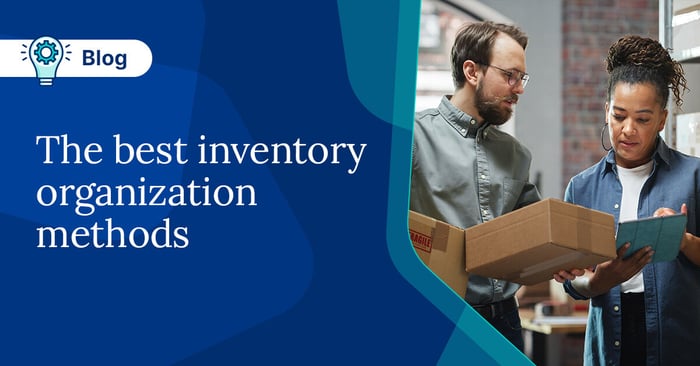
Inventory organization is the backbone of any successful product business. It’s often the difference between seamless operations and operational chaos. Strong organization strategies and tech tools make it possible to tame that chaos.
We’ll be exploring some inventory organization ideas that lead to improved accuracy, faster order fulfillment, reduced overhead costs, and a more streamlined operation.
What is inventory organization?
Inventory organization is the process of managing your stock so you can easily store, track, and retrieve products from your warehouse. It includes sorting inventory into categories, maintaining accurate records, making the most of your storage spaces, and leaning on technology to keep things running smoothly. When done right, it helps reduce errors and makes your business processes more efficient.
Imagine a warehouse where each storage area is marked with a unique SKU, designating different types of inventory products. This setup allows workers to quickly find what they need, whether shipping orders or restocking shelves. By organizing items like electronics in one spot and clothing in another and using tech tools to track it all, the warehouse runs like a well-oiled machine.
Best ways to organize inventory
Our six warehouse organization strategies emphasize best practices for streamlining inventory access and optimizing management throughout the product lifecycle.
1. Invest in an inventory management system (IMS)
No matter how many products you have, tracking every item’s location, quantity, and movement can quickly become complicated. Compound these issues with manual errors, and you have a recipe for inventory chaos, leading to lost sales, frustrated customers, and stock imbalances that could impact your company’s bottom line.
You need to invest in an IMS system like Cin7 that can:
- Automate data entry and calculations to minimize costly mistakes that lead to overstocks, stockouts, or incorrect orders.
- Provide detailed insights on sales trends and stock turnover rates.
- Streamline the entire inventory process, from receiving new stock to fulfilling orders. This frees up your staff to focus on other tasks like building customer relationships and analyzing sales data for insights.
Reduce inventory carrying costs by optimizing stock levels and minimizing waste.
2. Track inventory throughout its lifecycle
The inventory lifecycle covers the entire journey of a product, from procurement to sale. It often involves sourcing, storing, sales, shipping, financial transactions, and monitoring critical metrics like product expiration dates.
Effective inventory tracking ensures real-time visibility of your stock levels, preventing costly stockouts and overstock situations. An IMS with robust tracking capabilities provides the data you need to make informed decisions about purchasing, sales, and production. This enables efficient fulfillment of customer demand while minimizing excess inventory and associated carrying costs.
Let’s say you run a small business that sells artisanal soaps online. Initially, you track inventory manually, noting sales and restocks in an Excel spreadsheet. However, this method becomes unsustainable as your business grows. Orders increase, product variations multiply, and errors begin to multiply. You then decide to implement a robust inventory management solution like Cin7.
The system automatically updates stock levels in real time as sales occur and when new shipments arrive. By monitoring this data, you notice that lavender soap sells quickly, while oatmeal soap often remains in stock for months. Using these insights, you can adjust production rates and increase lavender soap production while reducing oatmeal soap to align better with customer demand.
This data-driven strategy prevents overstock of slow-selling items and ensures popular items are always available even during peak demand. The result? More efficient operations, satisfied customers, and a healthier bottom line.
3. Automate where possible
Manual processes can be tedious and error-prone, leading to issues like incorrect stock levels, missed orders, and delayed shipments. Despite these drawbacks, warehouse automation remains underutilized, with industry professionals estimating that less than 20% of warehouses have embraced automation.
Cin7 automates and streamlines your manual processes. It also reduces the likelihood of human error, such as miscounting stock or entering incorrect data. When you sell an item, Cin7 automatically updates the inventory levels across all integrated e-commerce channels like Shopify and eBay. That way, there’s no need for manual recounts or adjustments after each sale.
Advance Global, a wholesale provider of safety and compliance products, relied on manual processes to manage its business operations, which significantly hindered its growth. Implementing Cin7 Core eliminated those manual processes through automation and integration. This solution centralized ordering, receiving, and invoicing functions, while seamlessly connecting with Starshipit for customer shipments and Pinch Payments for managing overdue accounts.
This integrated tech stack not only streamlined Advanced Global’s processes but also gave them real-time insights into their operations, which helped them take advantage of growth opportunities and remain profitable.
4. Use accurate forecasting for better planning
AI-powered forecasting tools like Inventoro by Cin7 help you predict future product demand. Knowing what’s likely to sell and when lets you plan ahead and avoid costly inventory mishaps such as understocking for peak sale periods.
Inventoro’s insights also help you adjust to seasonal demand shifts so you’re well-prepared for changes in buying behavior — think swimsuits in the summer and warm sweaters during winter. Plus, you can capitalize on viral products and quickly adapt your inventory to meet the unexpected surge in demand.
These precise demand forecasts empower you to leverage bulk purchasing discounts and negotiate favorable terms with suppliers. You can confidently place large strategic orders for high demand products. Manufacturers can also plan production schedules to avoid rushing to meet unexpected demand or having excess inventory sitting idle.
5. Conduct regular inventory audits
Even with the most sophisticated software in place, discrepancies can still creep into your inventory records. Regular audits act as a reality check, ensuring that what’s in your system matches what’s physically in your warehouse.
Conducting an inventory cycle count instead of doing an entire inventory count will help you minimize disruptions to business operations.
Consider a sports equipment store with an extensive inventory, ranging from basketballs to yoga mats. Instead of shutting down for a full day or more to count every item, the store can opt for cycle counting. This strategic approach involves counting specific product categories on a rotating schedule — for instance, tallying basketballs one week and yoga mats the next.
By systematically auditing different inventory sections on a rotating basis, the store can monitor its stock regularly without interrupting daily sales activities. This system helps ensure inventory accuracy and allows for quick adjustments in case of discrepancies.
6. Optimize your inventory storage layout
Optimizing your warehouse layout allows your team to quickly locate and retrieve items, more quickly fulfilling orders. It also makes it easier to conduct inventory counts.
So, how do you organize your warehouse effectively? The best practice is to divide it into zones based on product categories, picking methods, or other relevant factors to simplify navigation and improve efficiency. Use a clear and consistent labeling system for shelves, bins, and products to make it easier for employees to locate items.
Cin7 Core’s user-friendly warehouse management technology offers robust pick-and-pack features designed to streamline warehouse operations. The system uses barcode technologies and wireless scanning to enhance the accuracy and speed of the picking process. It guides your warehouse team on the quickest picking routes, slashing the usual walking time by up to 40%.
How Cin7 helps with inventory organization
Cin7 is an intelligent commerce platform that boosts warehouse efficiency for product businesses. Some of its key features include:
Comprehensive inventory management software
Cin7’s robust software provides real-time tracking of stock levels, orders, and sales in real time across multiple channels.
You can see how every product moves from one location to another, including:
- Monitoring items from dock arrival to inventory placement
- Track supplies throughout any internal manufacturing
- From the warehouse to brick-and-mortar locations
- Return receipt and restocking
Cin7 helps you identify and eliminate bottlenecks and optimize your inventory flow for maximum efficiency.
Accurate forecasting
Inventoro by Cin7 offers precise AI-driven forecasts and daily performance updates. This technology helps you monitor your products’ performance in real time and adjust your inventory strategy.
With additional insight into your consumer demand, you can prevent overstocking (that ties up capital and storage space) and stockouts (that lead to lost sales opportunities).
Automation
Cin7 helps you create automated tasks, reports, workflows, and notifications, such as invoice approvals and payments. This saves labor and time in all your inventory and accounting processes.
Warehouse management
Cin7 unites your back-end warehouse and shipping operations so you can receive, process, and fulfill orders efficiently. It also helps you reorder easily and avoid stockout headaches.
Seamless integration with accounting tools
Cin7 integrates with accounting systems like Xero and QuickBooks, allowing you to automatically create entries and synchronize bills, payments, and invoices. You no longer have to manually match transactions and financial records, simplifying workflows and improving data accuracy across your business.
Organize your inventory efficiently with Cin7
Effective inventory organization optimizes your operations and maximizes your business’s potential. But you need a comprehensive solution that brings all these strategies together for the best inventory control.
As an intelligent commerce platform, Cin7 provides the tools you need to organize your inventory efficiently, streamline your operations, and stay ahead of the competition.
Start your free trial with Cin7 today and watch your business thrive.
More from the blog
View All Posts
COGS: What it means for different business stages
Read More
Choosing the Right E-commerce Integration: Key Factors for Business Success
Read More