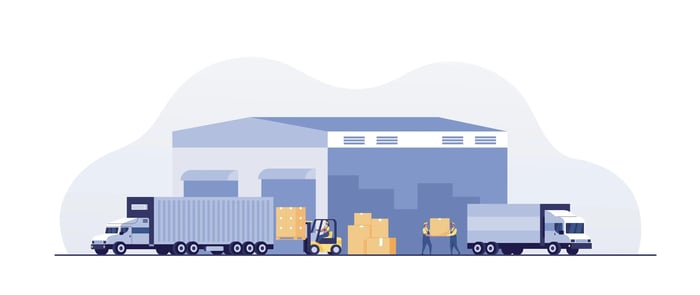
The global supply chain is growing at a tremendous rate, putting pressure on wholesalers and retailers to get more mileage out of their warehouses. These giant storerooms must hold more inventory, and stock has to be processed faster. A good way of achieving this is by adopting a lean method of warehouse management.
What is the lean approach?
Developed by Toyota for its auto manufacturing plants, the lean approach is all about paring processes down to a minimum, leaving only what’s necessary and essential in place. When applied properly and strategically, a lean approach can significantly reduce costs. It can also improve customer satisfaction.
What is lean warehousing?
Just as the lean approach cut out anything unnecessary in Toyota’s manufacturing plants, in a warehouse, it means having the least amount of inventory to satisfy demand while streamlining processes to ensure there are no extra steps.
In addition to reducing overall cost and increasing efficiency, lean warehousing also leads to more accurate control over inventory. With such control in place, the whole supply chain runs smoother and more efficiently, and customers get their products in good time.
Here are a few more ways lean warehousing helps retailers and wholesalers:
- Provides better visibility into warehouse activities,
- Enables quicker decision-making,
- Reduces lead times,
- Improves operational efficiency,
- Ensures the accuracy of data, and
- Reduces unnecessary inventory.
How does the lean approach reduce waste in a warehouse?
Less wasted inventory
With the lean method, a warehouse stocks a bare minimum of inventory, holding only what’s going to be used or sold in the near term. As a result, there’s less chance of a company being left holding stock it can’t sell.
More cost-effective transportation
Here, the lean approach means finding direct routes when making deliveries. To meet customer expectations, transportation should be aligned with customer service so the entire transportation process becomes smooth and cost-effective.
Efficient flow of inventory
The route taken by inventory in a warehouse should be the quickest and most effective. This route goes from collecting the items to getting it to the packing department and the packing process itself. In other words, every time inventory moves from one area to another, it should only be in the service of the actual fulfillment process. This also eliminates the time inventory sits in the warehouse.
A system is overprocessed when it has steps in it that have no direct purpose. Those steps are a waste. By applying lean warehousing principles, the whole process can be analyzed and tracked to ensure that every action taken is there for a reason: to fulfill orders as fast as possible.
No more paper
Lean principles make the warehouse go paperless. That means no paper pick tickets, packing slips, or other such paperwork. Lean warehousing shifts all these forms to electronic devices like cell phones, computers, and tablets. This can lead to big savings over time, while cutting down manual errors.
What are the five S’s of lean warehousing?
There are five practices that have to be paid attention to with the lean method. Each is equally important, and each begins with the letter “S.”
Sorting
This is about stock control, making the best use of the inventory. You should:
- Remove damaged, outdated, surplus, broken and defective stock from the warehouse.
- Only move inventory around the warehouse when it’s necessary.
- Automate inventory control, logging it in and tracking its movement with electronic devices like scanners.
Straightening
When you’ve sorted out the stock, you have to make sure it’s organized in the best way.
- Place frequently used items in areas that are easy to get to.
- Clearly label the inventory, and tag everything.
- Put up signage that clearly shows where everything is and gives directions to get to it.
Shining
This is about the whole facility being clean and tidy. When the warehouse is well-maintained, efficiency is increased and accidents are reduced. When applying shining, you need to do the following:
Have the warehouse cleaned after every shift.
- Maintain hygiene in the warehouse.
- Place garbage cans everywhere to prevent littering.
Standardizing
In a warehouse, all employees and managers should follow the same procedures to ensure the warehouse is run well. Warehouses are standardized in the following ways:
- Set standards and clearly defined processes that help weed out ambiguity.
- Make all the standards easily accessible to the staff.
- Translate processes and procedures into simple pictures, and place them visibly around the warehouse.
Sustaining
Sustaining means making sure good operational procedures and processes are continued over time. Here’s what you need to do:
- Implement behaviors and habits that will maintain standards in the long run.
- Frequently evaluate success by conducting regular audits and reviews.
- Follow up on creative ideas from the employees, and use them when they’re good ones.
Make your warehouse lean with Cin7 Omni
If you’d like to introduce lean practices into your warehouse, take action and get in touch with a warehouse management team that knows the method inside out. At Cin7 Omni, we’re confident in our ability to streamline your warehouse processes and can help you implement all of the five “S” operations.
Reach out to our team today, and let us help you eliminate warehouse waste, cut down overall costs and optimize your warehouse operations. Book a demo with our experts now! We are all eager to assist you.
More from the blog
View All Posts
Cin7 Leads the Way: Groundbreaking Updates and Innovations in Inventory Management
Read More
Our new ISV partners
Read More