How to manage inventory for planned and unplanned plant shutdowns
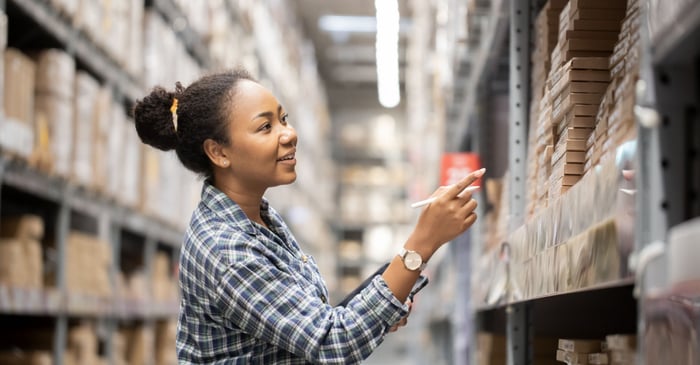
Although not very often, factory shutdowns happen. Whether planned or unplanned, shutdowns cause major disruptions and financial losses, and therefore, you must understand how to deal with them.
Planned plant closures are usually for maintenance purposes. Essential to keep machinery and equipment in good working order, they usually happen once or twice a year. During these inspections, repairs may be made, worn-out parts may be replaced, and upgrades or new machinery may be introduced.
Unplanned plant closures usually result from sudden power outages and machines breaking down. An unannounced strike is another reason. A drop in demand can also be a cause. And in a worst-case scenario, a production line will close down when the facility runs out of raw material — more on that later.
Knowing that a plant will shut down at some point means you can plan for the event, and with pre planning in place, negative impacts can be mitigated. The best pre planning involves inventory control, and that’s what we’re going to examine here.
Managing inventory to prevent or mitigate a shutdown
Here are things you can do:
Limit inventory before a planned shutdown
When you know you’re going to have to shut your operations down, either for scheduled maintenance, upgrades, or audits, you can ease the pain by reducing the level of stock you’re holding beforehand. Keeping inventory has its own costs: A workforce has to maintain it, and capital is tied up in it. So if you make sure you only have the least amount you can get away with, literally only what you need to restart, you’ll cut down on expenses and mitigate the losses the shutdown creates.
Prepare for unplanned shutdowns by limiting inventory
A good way of mitigating the effects of an unplanned closure is to have a lean inventory management system in place. As the name implies, this system is all about getting rid of waste, unneeded excess. For inventory specifically, it’s about having only as much as is needed at any given time. The system operates on the “pull” system where inventory is “pulled in” when needed, as opposed to the “push” system that always has more stock than is needed and “pushes” it out.
Introduced by Toyota in its manufacturing unit in 1950, and later explored in the book Lean Thinking: Banish Waste and Create Wealth in Your Corporation by James Womack and Daniel Jones, lean inventory management keeps stock at minimal levels, so if an unplanned shutdown happens, the company is prepared and losses can be controlled.
Lean inventory management puts stock into three categories, A, B, and C, each one based on the items’ cumulative annual consumption value. The annual consumption value is arrived at by multiplying the number of units sold in a specified time, say a year, by the cost per unit. When that’s been worked out, a company will know exactly which items have the most value for them and can organize their storage and oversight appropriately.
- Category A: Pricier items. Though typically making up only 20% of a company’s stock, these more expensive items usually account for 70% of items used when the annual consumption value is applied.
- Category B: Less pricey, the items here usually account for 25% of the total annual consumption value.
- Category C: These least pricey items account for 5% of the annual consumption value.
Inventory management software like Cin7 can easily work out annual consumption values and do the categorization for you.
Prevent shutdowns caused by stockouts
It’s possible for raw materials to run out and cause a shutdown. Maybe an error was made in counting the number in storage; maybe a supplier didn’t deliver; maybe there was an issue with the supply chain. Whatever the reason, you can make sure you’ll be able to cover for these situations by having buffer stock. Buffer stock is a little bit extra for emergencies. The amount of buffer stock a company holds has to be carefully weighed. Too much and it’ll be a drag on company outlay; too little and it might not be enough to cover your needs. An inventory management system like Cin7 can solve this conundrum.
Reasons for shutdowns, and best ways to plan your inventory levels
Shutdowns are caused by specific events, and in order to plan your inventory levels, you have to have a good idea which ones are more likely to happen to you. Consider the following scenarios:
- External factors: If a shutdown is likely to happen because of bad weather, a natural disaster, government regulations, or a strike, you should have buffer stock on hand.
- Internal factors: Here we’re talking about a power outage or machines breaking down. For machine breakdowns, spare parts should be readily available at all times. For inventory, there has to be enough available to restart production.
Cin7 can analyze your data quickly and help identify which inventory control method is best for you.
The final analysis
Factory shutdowns, whether planned or unplanned, cause unwanted stoppages that will affect the bottom line. When it comes to inventory, there are ways to mitigate these losses and help you ride the closures out.
Cin7 is a good way to help you figure out the best way to manage your inventory. To find out more, click here to schedule a live demo with one of our experts.
More from the blog
View All Posts
10 best software solutions for small business management in 2024
Read More
Free, streamlined packing slip templates for 2024 [Printables]
Read More