Reducing manufacturing waste: 11 strategies for small businesses
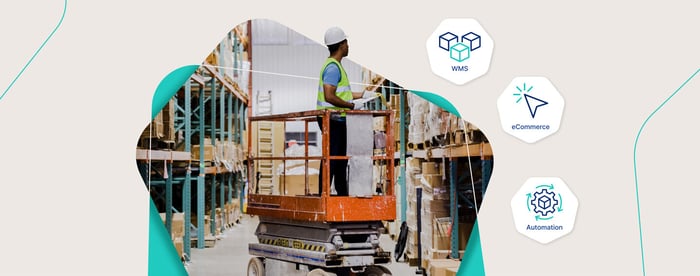
Have you ever hosted a dinner party just to discover that you have a week’s worth of leftovers at the end of the night? Waste, in principle, is a natural part of building or creating something. In manufacturing, however, you can’t put waste in Tupperware and have it for lunch the next day. In business, the consequences of waste have compounding effects that can negatively impact your bottom line.
The results of manufacturing waste are extreme. Inventory and manufacturing waste total an average loss of $163 billion annually, mainly due to human error in inventory management and manufacturing.
So how does manufacturing waste happen? And what exactly is classified as waste? Waste isn’t always the inventory that doesn’t make it to the customer’s door; it’s also the processes that don’t add any value to the customer. However, some activities, while considered waste, are vital to the production process.
You can assess waste in two ways:
- Product development: Waste that directly impacts revenue but is essential. For example, production planning, quality testing, creating warehouse reports, etc.
- Pure waste: Waste that doesn’t add value and is unnecessary. For instance, waiting for someone to finish using a machine before you can use it.
In this post, we’ll explore the different types of waste, strategies for reducing it, and how cutting waste can have significant, and sometimes unexpected, benefits for your growing business.
Key Takeaways:
- In lean manufacturing, waste is broken down into 8 specific types: inventory, transportation, waiting, motion, overproduction, defects, overprocessing, and underutilized staff.
- Companies employ many different strategies to reduce manufacturing waste, like optimizing warehouse layouts and implementing closed-loop systems.
- The benefits of reducing waste include cutting costs, enhancing efficiency, and gaining a competitive advantage.
- Using a top ERP software for manufacturing can help you make smarter inventory decisions that help in cutting waste.
What are the types of manufacturing waste?
When companies examine ways to reduce waste, many look to the lean methodology — a philosophy of continuous improvement rooted in finding and removing waste in workflows. Lean methodology divides waste into eight specific types:
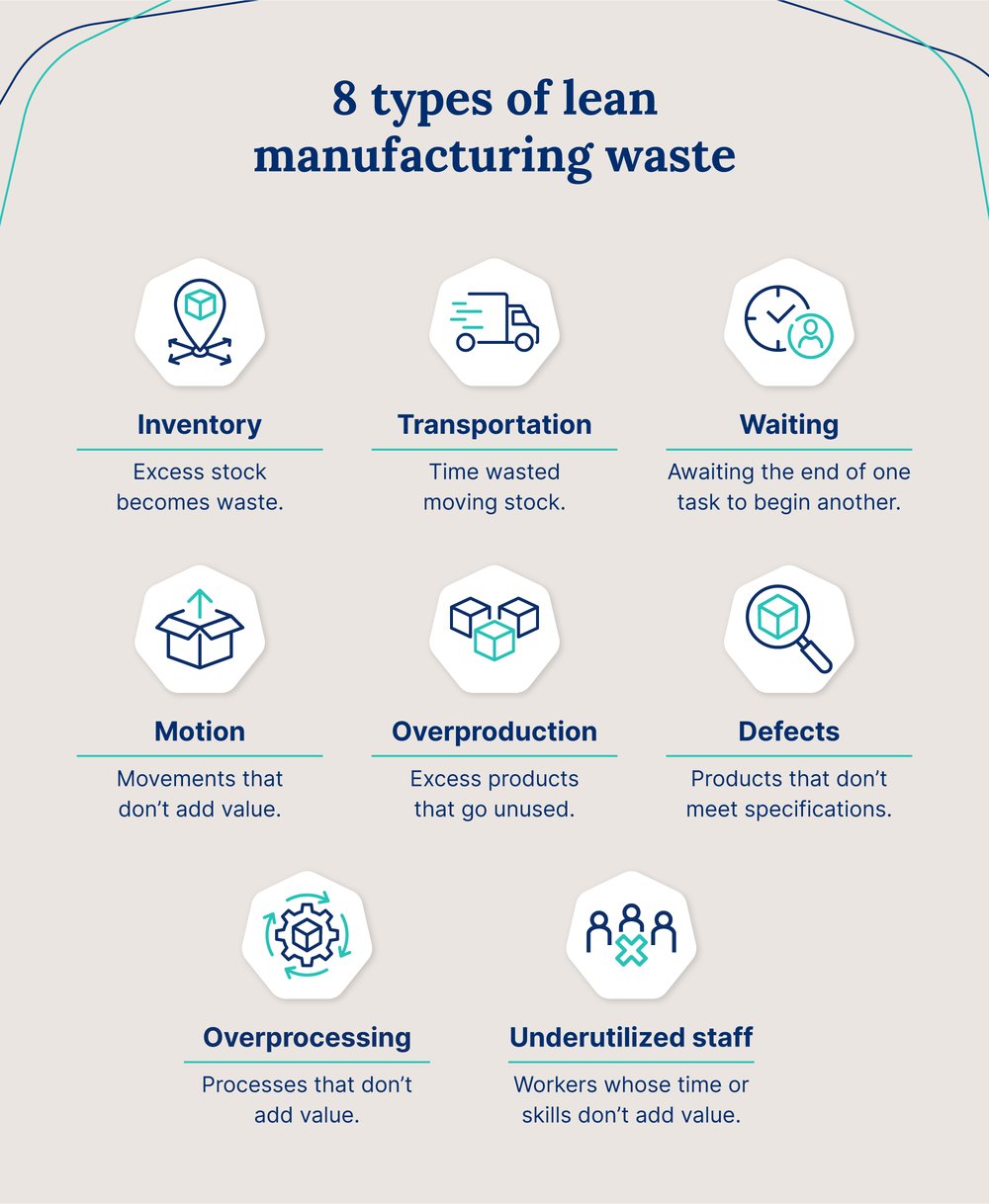
- Inventory: Excess stock that becomes waste.
- Transportation: The process of moving stock from one place to another.
- Waiting: The time a human or machine has to wait for the completion of one task to start another.
- Motion: Unnecessary movement that could be used for another purpose.
- Overproduction: Excess products that go unused.
- Defects: Products that don’t meet customer specifications and have to be discarded.
- Overprocessing: Processes that don’t directly deliver value to customers
- Under-utilized staff: Workers whose skills or time don’t deliver value to customers.
As you can see, manufacturing waste is not always scrap materials. It can also take the form of unused or misused time and resources.
How to reduce manufacturing waste
Now that we’ve defined manufacturing waste, how can small businesses reduce it? Remember, some waste is necessary to achieve the end result, so manufacturers can never totally eliminate waste.
However, there are strategies businesses can employ to reduce waste as much as possible. Here are 11 proven methods for success:
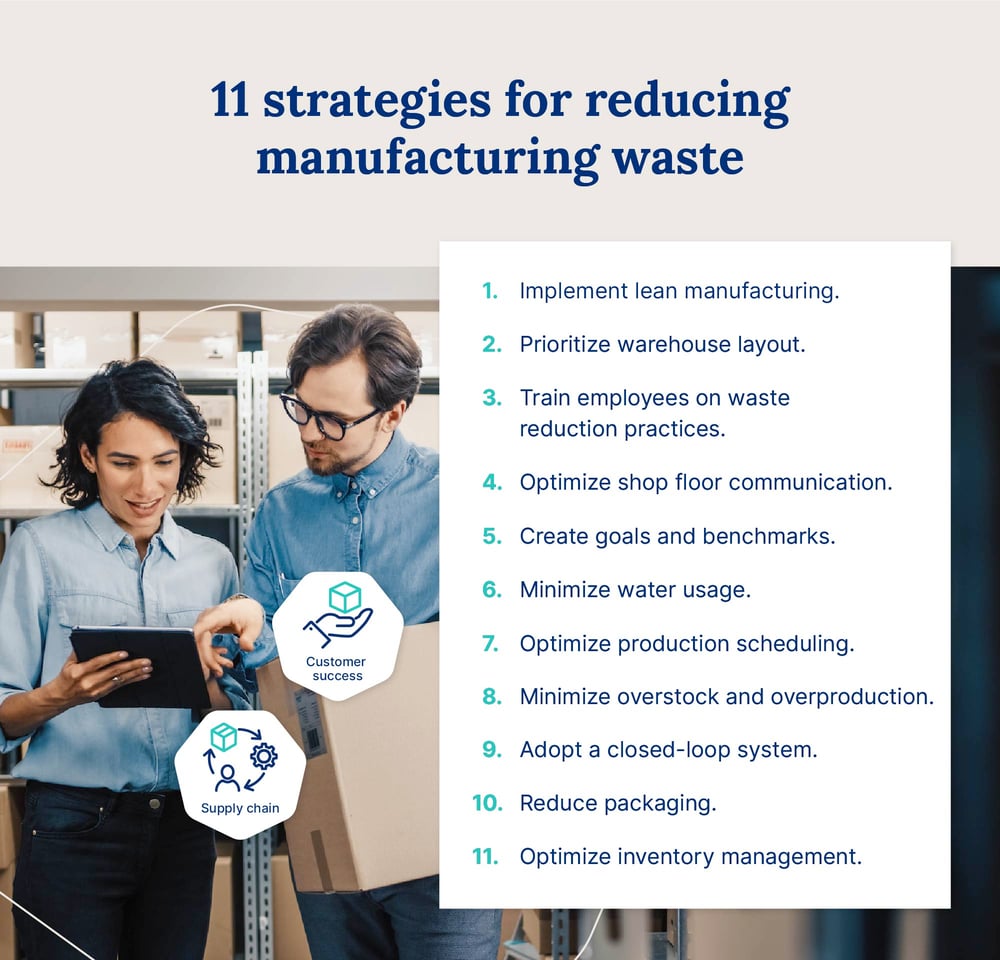
1. Implement lean manufacturing principles
The idea behind lean manufacturing, or lean warehousing, is to maximize efficiency by reducing all efforts and resources that don’t drive value to the customer.
Under lean principles, every aspect of the manufacturing process is examined under a microscope to pinpoint where inefficiencies stem from. Some improvements that may come from implementing lean principles may include:
- Reorganizing machines for maximum efficiency.
- Reevaluating employee schedules to ensure everyone delivers value while on the shop floor.
- Rewriting processes to eliminate any gaps in efficiency.
2. Prioritize warehouse organization
In manufacturing, warehouse design is critical. Warehouses should always be well-marked and organized so shop floor workers never miss a beat.
Clearly mark all the locations of assets throughout the warehouse, including:
- Inventory
- Supplies
- Tools
Over time, the markings may fade, become nonexistent, or obsolete. Worn signage may not affect longtime employees, but new hires and temporary workers may have difficulty navigating through a warehouse that isn’t marked or organized. When performing your regular waste audits, prioritize clear labeling.
Cin7 Core’s WMS app takes the legwork out of warehouse organization for businesses. With our advanced features, you can create dedicated zones, draw out walking paths, and more. With all this information available, you can easily visualize your most efficient warehouse layout.
3. Train employees on waste reduction practices
Businesses can create waste reduction processes and train employees on them so everyone is aware of the little ways they can reduce waste on the shop floor.
For example, businesses can establish standard operating procedures in the warehouse so everyone knows the expected quality and quantity of products during production. If everyone is sufficiently trained on the standards, waste is far less likely.
4. Optimize shop floor communication
Seamless communication on the shop floor is also key for ensuring everyone has the most up-to-date information regarding product specifications. Inefficient communication can lead to defective products and wasted time.
Easy ways manufacturers can pass information to the shop floor include:
- Daily meetings.
- Automated reporting.
- Quick debriefs between shifts.
5. Create goals and benchmarks for waste reduction
Attaching a specific benchmark to a goal makes it much easier to track progress and see how far you have to go realistically.
Example: If your company’s goal is to reduce waste, put a measurable value behind it.
- Calculate the amount of waste you’re currently seeing and try to reduce it by 15% before the end of the quarter.
- If you fall significantly short of that, your processes may need an overhaul.
- If you fall just below it, you know you’re trending in the right direction.
6. Minimize water usage
Wastewater and industrial sludge comprise a significant portion of manufacturing waste streams. You can reduce them by minimizing water usage in the operations.
You can do this by substituting water with:
- Chemical drying agents.
- Dry machining.
- Reverse osmosis.
- Utilizing a membrane biological reactor system.
You can also encourage employees to reduce bottled water, as plastic drinking bottles comprise a major portion of plastic waste. Switch to drinking water in glasses or promote using reusable bottles in the workplace.
7. Optimize production scheduling
If you can streamline production schedules, you can cut back on wasted time. The best inventory management software includes automated demand forecasting as a built-in feature, so you can schedule accordingly and prevent unplanned downtime.
Once you know what demand looks like, you can create optimized schedules and ensure time and energy never goes to waste.
Watch our webinar on how to prepare for seasonal demand.
8. Minimize overstock and overproduction
Overstock and overproduction are perhaps the most common types of manufacturing waste. A great way to limit this type of waste is by implementing a just-in-time inventory system.
In a just-in-time system, manufacturers order raw materials from suppliers right before production begins. By waiting until the last minute to order these materials, manufacturers can keep production levels low, reducing the chance of obsolete inventory and deadstock.
9. Adopt a closed-loop manufacturing system
Green chemistry, or designing materials to reduce hazardous waste, is an excellent technique to reduce waste generated by various processes, but if that’s not a viable solution, consider a closed-loop manufacturing system.
A closed loop helps you:
- Keep track of inventory.
- Utilize recycled materials in the production cycle.
Closed-loop systems extend the life span of chemicals by maximizing their efficiency. It helps reduce contamination and minimizes the amount of new chemicals you need to purchase.
10. Reduce packaging
Redesign product packaging and ensure it uses the minimum amount of materials. Incorporate recyclable or reusable packaging content, such as air packs or corn-based packing peanuts, for cushion.
Buying products in bulk can also help reduce your overall packaging volume.
11. Optimize inventory management
Connected inventory performance isn’t just about quickly getting products to customers. It’s also about managing inventory in an efficient and growth-oriented way — and waste is often the enemy of growth.
By optimizing your inventory management through comprehensive software, you can see where waste is coming from and then take the necessary steps to reduce it. While sometimes waste is apparent, other times it’s harder to find. An end-to-end tool can provide a broad look at your inventory processes and help you determine where to improve.
Request a demo of Cin7 to see inventory performance in action.
Benefits of waste reduction
Minimizing waste provides several significant benefits for a business, some more obvious than others. Here are a few well-known, and some lesser-known, benefits of cutting back on manufacturing waste:
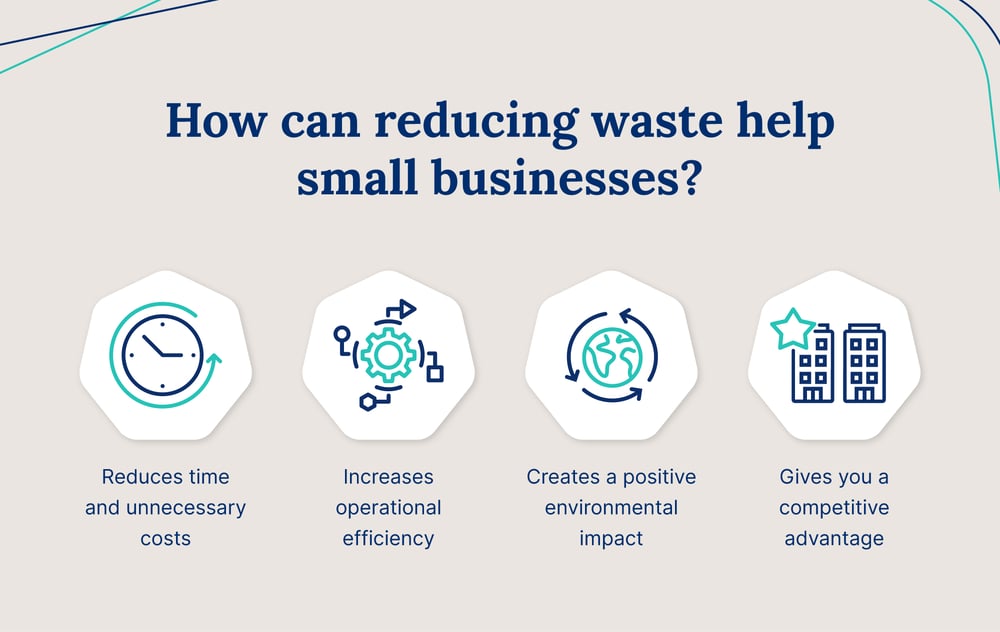
Reduces time and costs
Spending money on something you don’t need or don’t use is never good. Analyzing your manufacturing processes to see where waste is happening can help you significantly reduce costs — whether it’s on materials, labor, or both.
By creating a process built to prevent waste, you can also save time as you enjoy a more hands-off approach to inventory management. With all this time back, you can focus on the more important tasks, like growing your business.
Increases operational efficiency
Reducing waste doesn’t just mean cutting down on obsolete inventory — it also means filtering out the processes and time that don’t drive value.
Once you determine where the waste stems from, you can make changes that lead to more efficient processes. This might mean:
- Reevaluating your warehouse design for optimal efficiency.
- Reducing the amount of labor at a given time.
- Cutting back on repetitive QA processes.
Determining and deleting inefficiency can help you produce faster and grow quicker — with less money spent.
Creates a positive environmental impact
Overproduction and over processing can have a damaging environmental impact and should be avoided as much as possible.
Reducing packaging waste or using recycled materials can benefit your company’s production and its commitment to sustainability, giving you a competitive advantage in both growth and reputation.
Gives you a competitive advantage
It’s not common that companies will go the extra mile in reducing manufacturing waste. If you commit to prioritizing inventory control, performing waste audits, making efficiency changes, and reevaluating your processes, you can likely set yourself apart in your market.
How Cin7 can help
Waste is often hard to recognize, especially if you’re a growing business that has to focus on various other business items. However, adding automation to your inventory processes can help you glean where your inefficiencies lie and where waste is prominent.
Connected inventory performance allows businesses to see inventory from a bird’s-eye’s view and easily dig into where they can make improvements. With demand forecasting, reordering, and more done for you, you can create an inventory management machine impervious to waste.
Start a free trial of Cin7 to start reducing waste today.
More from the blog
View All Posts
Kanban in manufacturing: 9 major benefits [+examples]
Read More
Connected Inventory Performance: The Evolution of Inventory Management
Read More