How to select the right warehouse management system for your business
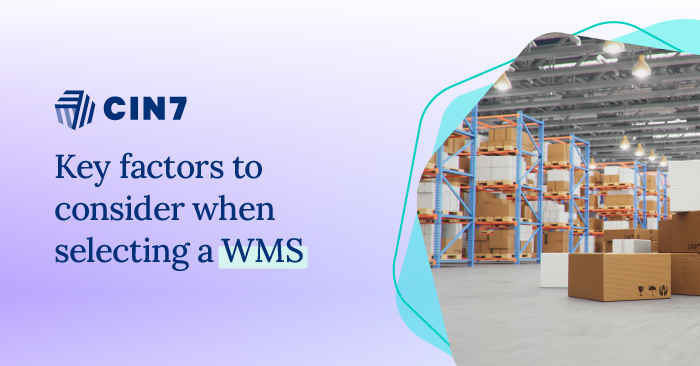
Warehousing is a critical component of the supply chain, providing a crucial link between production and distribution. The warehouse is where goods are stored after they have been produced or procured before they are dispatched to customers.
Proper and efficient warehousing helps ensure that products are readily available when needed, supports efficient order fulfillment, and can even help businesses reduce operational costs.
A key tool in achieving an optimized warehouse setup is a warehouse management system (WMS). In this comprehensive guide, we’ll tell you everything you need to know about WMS including the main benefits and the key features to prioritize when looking for an appropriate option for your business.
What is WMS?
A Warehouse Management System (WMS) is a software solution that helps companies streamline and optimize the day-to-day operations of their warehouses.
It provides businesses with real-time visibility on inventory levels, stock movements, and order statuses. This visibility ensures that businesses have a clear picture and understanding of what’s happening within their warehouses at any given time, which in turn allows them to make informed decisions both quickly and accurately.
A WMS also helps businesses coordinate and manage key processes such as receiving goods, order picking, packing, shipping, and handling returns. Furthermore, it helps them plan and allocate resources like labor and warehouse space more effectively.
The global WMS market has grown immensely in the last couple of decades as companies seek to improve efficiency in their warehouse operations. As of 2023, it was valued at $3.95 billion. It’s expected to reach $13.34 billion by 2030.
Why businesses need WMS
Businesses of all sizes, including SMBs can significantly benefit from implementing a WMS. Let’s discuss some of the primary benefits.
Improved inventory accuracy
Maintaining accurate inventory records is a common challenge in warehouse management. Many businesses still rely on manual tracking methods, which are susceptible to errors like miscounts, incorrect data entry, and misplaced items. These errors can lead to costly issues such as stockouts or overstocking.
Stockouts result in missed business opportunities, while overstocking ties up capital, consumes valuable warehouse space, and increases the risk of product obsolescence or spoilage.
A WMS streamlines and automates inventory tracking through integration with technologies like barcoding, RFID, and sensors. This provides a constant, accurate picture of stock levels, locations, and movements within the facility. Accurate inventory data helps businesses make informed decisions regarding production (or procurement) and order fulfillment.
Faster order fulfillment
Today’s consumers expect fast and accurate order delivery. Indeed, the faster you fulfill your customer’s orders, the more likely they are to come back for repeat business and remain loyal to your brand. A WMS accelerates order fulfillment by optimizing various steps in the process, including picking, packing, and shipping.
For example, the best WMS solutions come with features like advanced order-picking algorithms, which prioritize orders based on factors such as delivery urgency, item location, and order size. Meanwhile, batch-picking or wave-picking features in WMS can group similar orders to minimize travel time within the warehouse. In addition, a WMS can generate packing slips and shipping labels automatically, further reducing the time spent on manual documentation.
The overall result? Faster, more accurate order processing that helps businesses meet delivery deadlines and improves customer satisfaction.
Reduced operational costs
Operational costs can eat into profit margins, especially when warehouse operations are inefficient. A robust WMS helps businesses cut costs in several key areas.
First, it automates inventory tracking, counting, and data entry, which not only reduces the need for manual labor, leading to significant cost savings but also frees up your staff to focus on more important activities that add value.
A WMS ensures that every available inch of warehouse space is utilized effectively. Through a WMS, businesses can increase their overall storage capacity without having to expand their physical warehouse or turning to third-party storage solutions, both of which can be costly.
In addition to these direct savings, a WMS also reduces the likelihood of costly mistakes like mispicked orders, returns, or shipping errors, which can all impact a business’s profitability.
Better decision-making and insights
The best WMS solutions include sophisticated inventory data analytics and reporting tools that offer valuable insights into every aspect of your warehouse operations. These insights can inform key business decisions that drive operational improvements and boost overall profitability.
For example, a WMS can help identify slow-moving inventory, allowing businesses to make informed decisions about stock rotation, promotional strategies, or even discontinuing certain products. It can also highlight inefficiencies in warehouse operations, such as bottlenecks in picking processes or delays in order shipping. Businesses can then take the necessary corrective actions.
What's more, data collected by the WMS can be integrated with other systems, such as ERP or CRM platforms, to provide a comprehensive view of business performance. This holistic perspective is particularly valuable when scaling operations and planning for future growth.
Key features to look for in a WMS
There are numerous WMS solutions in the current market but not all are created equal. When shopping around for a WMS solution, here are some of the key features to prioritize.
User-friendliness
Even the most powerful WMS can fall short if it’s difficult for your warehouse staff to use. An intuitive, user-friendly interface reduces the learning curve for employees, ensuring faster adoption and smoother day-to-day operations.
Real-time inventory tracking and visibility
A good WMS system should include real-time inventory tracking features. These features ensure that every stock movement — whether it’s a new shipment arriving, an order being picked, or a product being shipped — is tracked and updated instantly within the system.
Key technologies that enable real-time inventory tracking include barcode scanning and RFID technology, both of which allow you to track and record items as they move around the warehouse.
Real-time tracking provides you with comprehensive visibility into your inventory at all times, which can facilitate more-informed decision-making. Some WMS systems also offer advanced features such as inventory alerts when inventory drops below a set threshold and even automatic replenishment.
Scalability and flexibility
A WMS should be able to grow and adapt alongside your business, i.e. it should be scalable. Scalability ensures that the system can handle increased demands as your operations expand, whether it’s an increase in order volume, the addition of new warehouses, or diversification of product lines. And it should do this without sacrificing performance or requiring expensive upgrades.
Flexibility is equally important. You should be able to customize the WMS to your specific business model, processes, and workflows. In the same vein, the system should be able to support or accommodate any changes in your operational workflows or processes.
Availability on multiple devices
You can’t walk around the warehouse with a desktop computer and a good WMS should not be confined to a single desktop or workstation. Instead, it should operate seamlessly across multiple devices, including mobile phones, tablets, and handheld scanners.
This flexibility ensures warehouse staff perform tasks from anywhere within the warehouse without having to return to a central station to input data. This is particularly beneficial in multi-floor or multi-location warehouses.
For example, picking teams can use handheld devices to receive order instructions and update stock levels in the WMS directly from the warehouse floor. This can enhance productivity and enhance overall operational efficiency.
Similarly, supervisors and managers can monitor product movement, and inventory levels, review key metrics, or approve workflows from their handheld devices, even while they are away from their desks or even the business facility.
Vendor support and reliability
When evaluating WMS options, it’s also important to consider the vendor’s level of customer support, the resources they offer, and their reliability over the long term. Focus on the following:
- 24/7 customer support: Look for a provider that offers round-the-clock customer support, especially if your warehouse operates in different time zones or on a 24/7 schedule. Prompt resolution of technical issues, whether it’s a system glitch, hardware malfunction, or integration error, can prevent costly downtime and keep operations running seamlessly.
- Access to resources and training: A good WMS vendor should provide a range of support resources, including detailed documentation, FAQs, video tutorials, user forums, and even personalized training programs to ensure your staff can operate the system at full capacity.
- Proven track record of reliability: A good vendor should also have a proven track record of system reliability, with minimal downtime and consistent performance. Online reviews and customer testimonials can help you verify a vendor’s reputation.
- Regular updates: A reliable WMS vendor should provide regular software updates to keep the system current. These updates may include new features, performance enhancements, and security patches. Regular updates ensure your WMS evolves with technological advancements and remains aligned with your business needs.
Integration with other business tools
Your WMS should seamlessly integrate with your other business tools and systems such as ERP and inventory management software, CRM, accounting software, and ecommerce platforms. This integration enables automatic and efficient data exchange across systems, ensuring consistency and accuracy throughout your operations.
For example, synchronizing inventory data with an ERP system ensures that critical functions like procurement, finance, and sales are always working with accurate, real-time information.
Similarly, integration with e-commerce platforms ensures inventory levels are updated in real time across all sales channels. This prevents overselling, enhances customer satisfaction by providing accurate stock availability, and streamlines order fulfillment.
Comprehensive integration also fosters better collaboration across various departments in your organization.
Evaluating WMS options for your business
Selecting the right Warehouse Management System (WMS) starts with understanding the different types available. Here’s a breakdown of the most common WMS options, along with their pros and cons.
Cloud-based vs. on-premise WMS
Cloud-based WMS
Cloud-based WMS solutions are hosted offsite, often by a third-party vendor, and accessed over the internet. Since the software is hosted in the cloud, businesses don’t need to invest in expensive infrastructure or hardware upfront. Most operate on a subscription basis where you pay either an annual or monthly fee to use the system.
While on-premises solutions still take up a larger share of the market, there is a growing preference for cloud-based WMS solutions over on-premise systems, driven by cost reduction and faster implementation capabilities.
Pros
- Low initial costs: Requires minimal investment in hardware and IT infrastructure.
- Automatic updates: The vendor handles system upgrades and maintenance, ensuring you always have the latest features.
- Scalability: Cloud-based systems can be quickly expanded to handle more inventory volume without the need for expensive infrastructure upgrades or a major disruption to your workflow
Cons:
- Ongoing subscription costs: Although it reduces initial investments, the subscription fees of a cloud-based WMS can add up over time.
On-premise WMS
An on-premise WMS is installed on the company’s own servers and managed by in-house IT teams. This model gives businesses full control over their data and infrastructure, making it a preferred option for those with specific compliance or customization requirements.
Pros:
- Greater data control: Full ownership of sensitive data, which is stored onsite.
- Customization: Offers extensive flexibility for tailoring the system to unique business or operational needs.
- No ongoing fees: Once implemented, there might be no recurring subscription costs, which can translate into lower long-term expenses.
Cons:
- High upfront costs: Requires significant investment in hardware, software, and IT resources.
- Maintenance responsibility: The business is responsible for updates, security, and troubleshooting, which can strain internal IT teams.
- Limited scalability: Expanding the system to accommodate growth can be challenging and expensive.
Standalone vs. integrated ERP/IMS with WMS
Standalone WMS
A standalone WMS is a system that focuses solely on managing warehouse operations, including inventory tracking, order picking, packing, and shipping.
These systems do not have inherent integration with other business systems like ERP or inventory management systems (IMS). It’s ideal for businesses that need robust warehouse operations but don't require full integration with other functions like accounting, purchasing, or customer relationship management.
Pros:
- Specialized functionality: Standalone WMS solutions are specifically designed for warehouse operations, offering deep functionality and customization options tailored to your specific needs.
- Affordability for small businesses: Standalone solutions tend to be more affordable than integrated solutions. That can come in handy for smaller businesses with limited budgets.
- Ease of deployment: These systems offer quick implementation with minimal impact on other business functions.
Cons:
- Limited integration: Doesn’t automatically share data with systems like ERP or IMS. This separation can lead to inefficiencies in workflows, such as delayed data updates or siloed operations. Where integration is possible, it can be complex and costly.
- Inconsistent user experience: Since standalone WMS is separate from other tools, users might experience different interfaces and workflows, which can lead to confusion and inefficiencies.
Integrated ERP/IMS with WMS
An integrated WMS is a part of a larger Enterprise Resource Planning (ERP) or Inventory Management System (IMS) suite. This type of system connects warehouse operations directly to other functions within the business, such as sales, finance, procurement, and customer service. Integration across these systems provides a more unified approach to managing your entire business.
Pros:
- Data synchronization: Provides a single source of truth for all business data, eliminating data silos and improving accuracy.
- Streamlined processes: Automates data flow between different departments, reducing manual data entry and minimizing errors.
- Improved decision-making: Provides a holistic view of the business, enabling more informed decisions.
Cons:
Overkill for small operations: For smaller businesses, an integrated solution may offer more functionality than necessary, resulting in wasted resources on features you don't need.
By carefully evaluating your requirements and considering the pros and cons of each of the above options, you can make an informed decision that best suits your business.
Wrapping up: Why choose Cin7 for WMS integration
Selecting the right Warehouse Management System (WMS) is a pivotal decision that can significantly impact your business’s efficiency and growth. With countless options available, finding a solution that aligns seamlessly with your operational needs while offering advanced functionality is essential.
Cin7 provides an advanced inventory management software with a built-in warehouse management system that provides complete control and visibility over your warehouse operations.
With Cin7, you can seamlessly manage tasks such as receiving shipments, packing products, tracking inventory, and picking items. Our tool comes with a user-friendly interface, integrates with various barcode scanners, and offers mobile accessibility, ensuring employees stay connected and productive no matter where they are in the warehouse.
Sign up for a free trial today to see how Cin7 can help you optimize your warehouse operations.