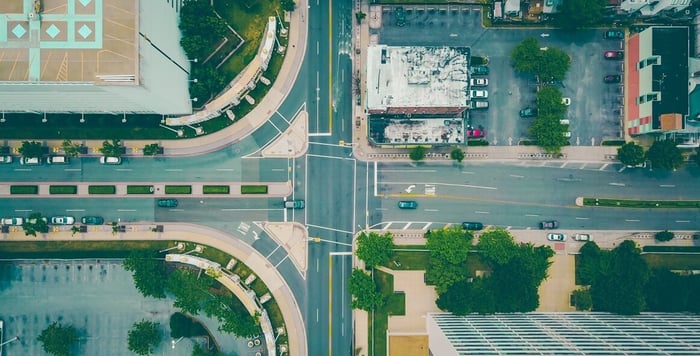
Experts have debated the virtues of global versus local supply chains forever.
Two UK-based procurement experts back in 2003 made valid points for both.
Local supply chains means lower transport costs, lower supply chain risk, greater sustainability.
Global sourcing offers more choice of suppliers and the best available prices. A local supply chain may not be more sustainable than a global supply chain. The procurement expert noted, that lamb production in New Zealand produced 25% less CO2 than UK-bred lamb, even factoring in transportation emissions.
Those considerations have not changed over the years. Cloud solutions make it easier than ever to manage supply chains regardless of geography or complexity.
Companies of any size can outsource manufacturing now just as easily as they can source materials from anywhere around the world.
Big apparel retailers have seen incredible cost reductions by using technology to bring overseas sourcing and production facilities closer together.
Some companies go further to make “local sourcing” part of their story. Research shows customers make purchasing decisions based on concepts of sustainability, natural resources, and corporate responsibility in labor practices. Local supply chains can make a strong argument in that appeal.
Going Local
You may have many good reasons to build local supply chains.
One supply chain expert writing in Forbes suggested we’ve entered an age of trade protectionism.
Big companies that outsourced production and stretched their supply chains across the globe face pressure to build local supply chains if nations start putting tariffs on imports.
Globalization may not be under immediate threat, but companies have plenty of good reasons to consider building local supply chains anyway.
Webb’s recommendations for developing local supply chains appear to apply more to large companies, big manufacturers with a lot of influence over suppliers.
He recommends companies look to developing local suppliers, encouraging them to collaborate or even merge in order to meet the company’s demand.
Other experts say it pays to research the suppliers in your local market, if you don’t work with them already, to learn if they can meet your needs.
More from the blog
View All Posts
Cost of goods manufactured explained: a guide for product businesses
Read More
Cin7 Partner Summit 2024: Celebrating success and innovation
Read More