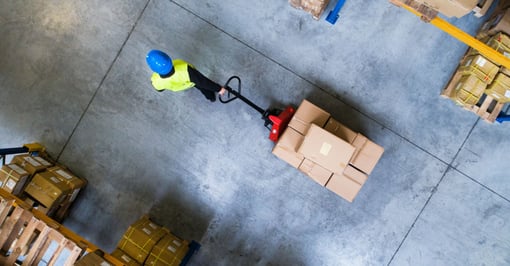
There’s more to running a warehouse than just piling inventory on shelves. The design of your warehouse can make or break your overall operational efficiency.
Warehouse layouts need to be optimized for clear visibility, smooth transfer of goods, and easy equipment accessibility. And no one design will work for everyone.
Most companies use one of three main warehouse layout styles. These layouts address items like the needs of different industries, the warehouse building size and shape, shipping and receiving volume, and budget.
So, what’s the best way to arrange your warehouse? Let’s dive into the options to help streamline your workflow and make the most of your warehousing space.
Here’s what we’ll cover:
What does warehouse layout mean?
Warehouse layout design factors
3 types of warehouse layouts for workflow
Best practices of warehouse layout design
What does warehouse layout mean?
Warehouse layout refers to both the physical structure of your warehouse and the many components within it. A proper warehouse layout also ensures workers have enough space to operate at maximum capacity, leading to a smoother inventory flow with less wasted time.
Warehouse layout design factors
There are several considerations for optimal warehouse design and workflow. You’ll want to consider all of them before deciding on the best space for your team.
Budget
Building a warehouse from scratch to custom specifications is expensive and time-consuming. While hiring a warehouse design expert to create a layout based on your requirements would be ideal, most companies need to work within a more limited budget.
Make sure to conduct a cost-benefit analysis and see which structures and equipment best fit your budget. You’ll also want to take existing warehouses into account. There might be an available warehouse space already on the market that’s a pretty good fit for your business needs. In many cases, warehouses for lease might already include some warehouse equipment like shelving.
Warehouse space needed
When planning your warehouse layout, how you divide the space determines your warehouse’s capacity and ability to store goods. For example, if you need to include office areas and break rooms, you’ll have less space to store and prepare inventory.
To maximize your warehouse’s storage capacity, make use of vertical space by stacking products. You can form clusters of products by grouping and stacking them together — which leads to quicker sorting later.
Equipment needed
To operate at full capacity, warehouse equipment such as shelving, conveyors, forklifts, lifting and packing tools, pallet racks, and safety equipment are required. Forklifts, in particular, are one of the most important pieces of equipment for warehousing operations, and you need to consider this tool’s cost and the space it needs to operate as you design your warehouse.
In addition to the equipment moving around, you’ll need barriers to protect your inventory and workers. Barrier rails work great when combined with mirrors and bollards. After analyzing your equipment needs, you can evaluate the best-suited warehouse layout and go from there.
Staffing requirements
Understanding staffing requirements can help you estimate how many people you’ll need and shift timings.
It’s important to make sure your warehouse’s layout does not impede the movement and productivity of your employees. The layout should also be designed while keeping the future in mind — you should have enough space so new employees, products, and materials can be added comfortably down the line.
Safety regulations
The safety of your employees is a prime concern. While designing your warehouse layout, ensure compliance with safety guidelines according to your local authorities and government.
This helps prevent both employee injuries and legal actions.
3 types of warehouse layouts for workflow
The three most commonly used warehouse workflow layouts are U-shaped, I-shaped, and L-shaped. Each style has benefits and drawbacks; let’s look at them in detail so you can determine the best possible structure for your needs.
The U-shaped warehouse flow
U-shaped warehouse flows are the most popular due to their simplicity and ease of replication. All the inventory is arranged in a “U” shaped semicircle, the middle portion (the bend of the “U”) is used for storage, and then shipping and receiving are performed at the ends of the “U.”
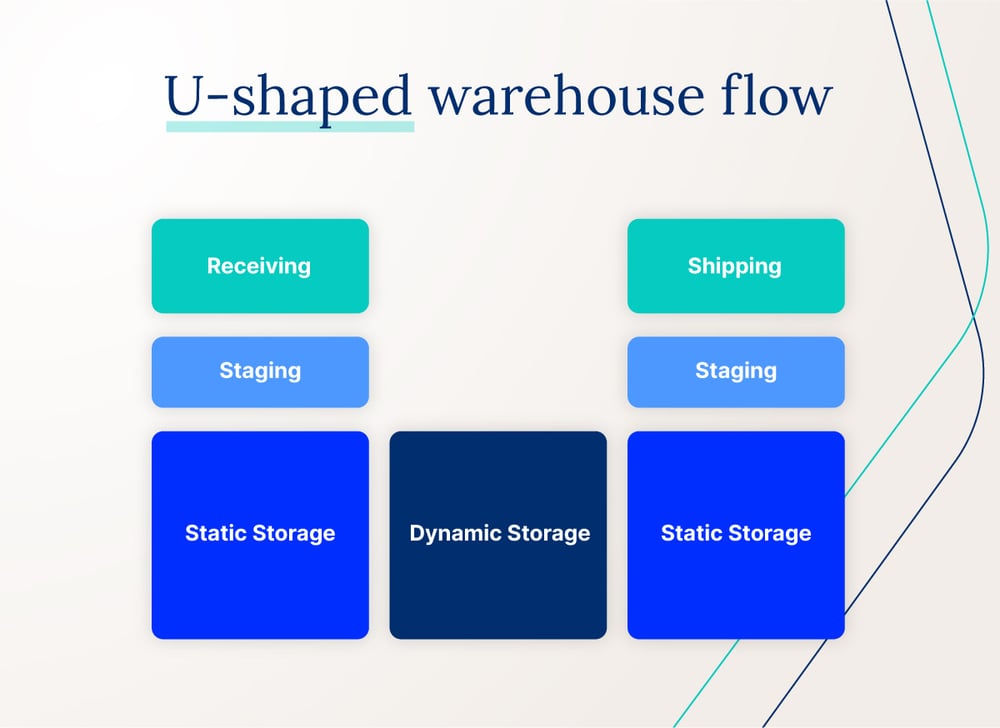
After receiving orders, products are placed in the staging or reception area to be sorted and then placed at appropriate storage locations. Storage locations are split into two categories:
- Static Storage is for slow-selling products that are more likely to sit on the shelves for a longer period of time.
- Dynamic Storage is for products with higher demand and turnover.
The “U” shape helps streamline inventory flow and keeps everything separate. By keeping incoming and outgoing shipments apart, the U shape also helps avoid bottlenecks.
Plus, because shipping and receiving are on the same end of the building, employees can swiftly move products between these two stages, and you may need less loading and unloading gear.
However, some people consider this a downside because the proximity of the entrance and exit can lead to congestion.
The I-shaped warehouse flow
The I-shaped warehouse flow is most often chosen by enterprise businesses that have larger warehouses. The I-shaped design offers a clear “in and out” view of product workflow for these bigger companies producing higher volumes.
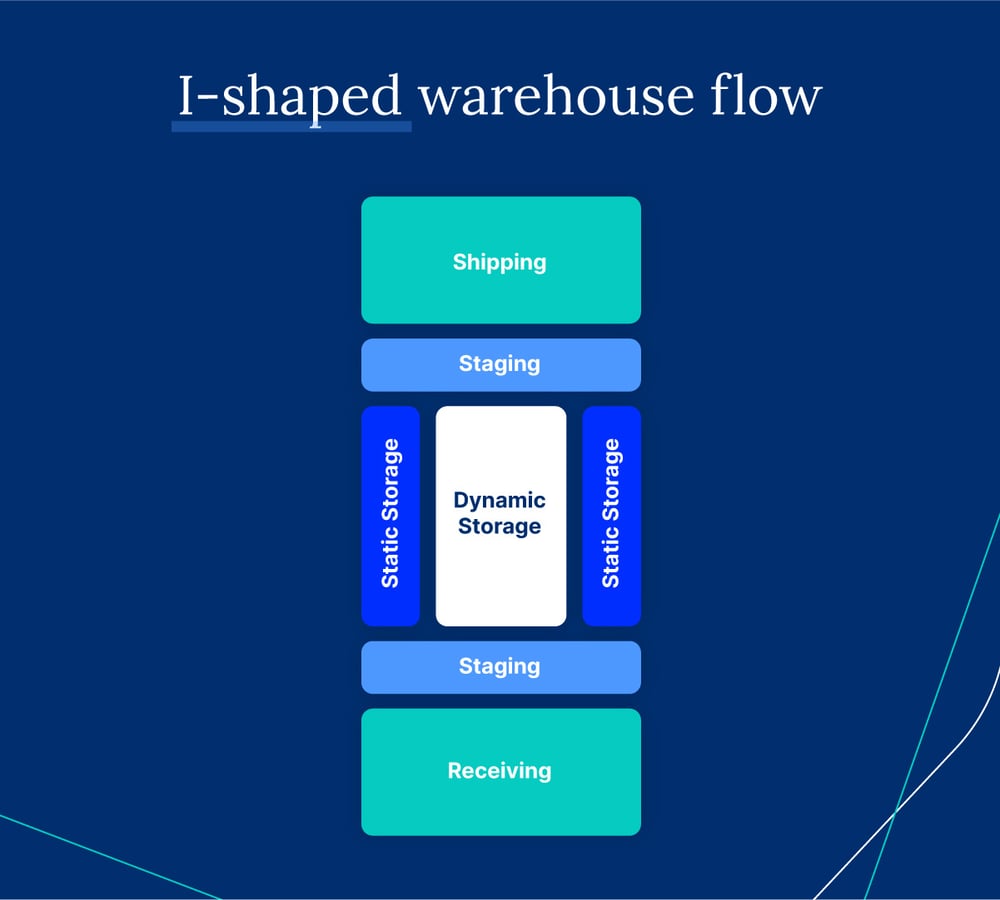
In this layout, receiving and unloading are on one end of the warehouse, storage is in the middle, and the shipping area is at the opposite end of the building. The I-shaped design allows for a linear flow from receipt to shipment.
From a bird’s eye view, the flow is similar to an assembly line, which both helps minimize bottlenecks and reduces back-and-forth movement.
The most significant drawbacks of an I-shaped warehouse design are that two sets of loading and unloading equipment are needed, and products must travel the complete length of the warehouse. With products being accessed on both sides of the “I,” you may also need a larger operational space for equipment like forklifts.
The L-shaped warehouse flow
For “L” layouts, the receiving and unloading areas are on one side of the warehouse, and the shipping and picking areas are on an adjacent side, creating a 90-degree angle. The remaining space is then designated for storage purposes.
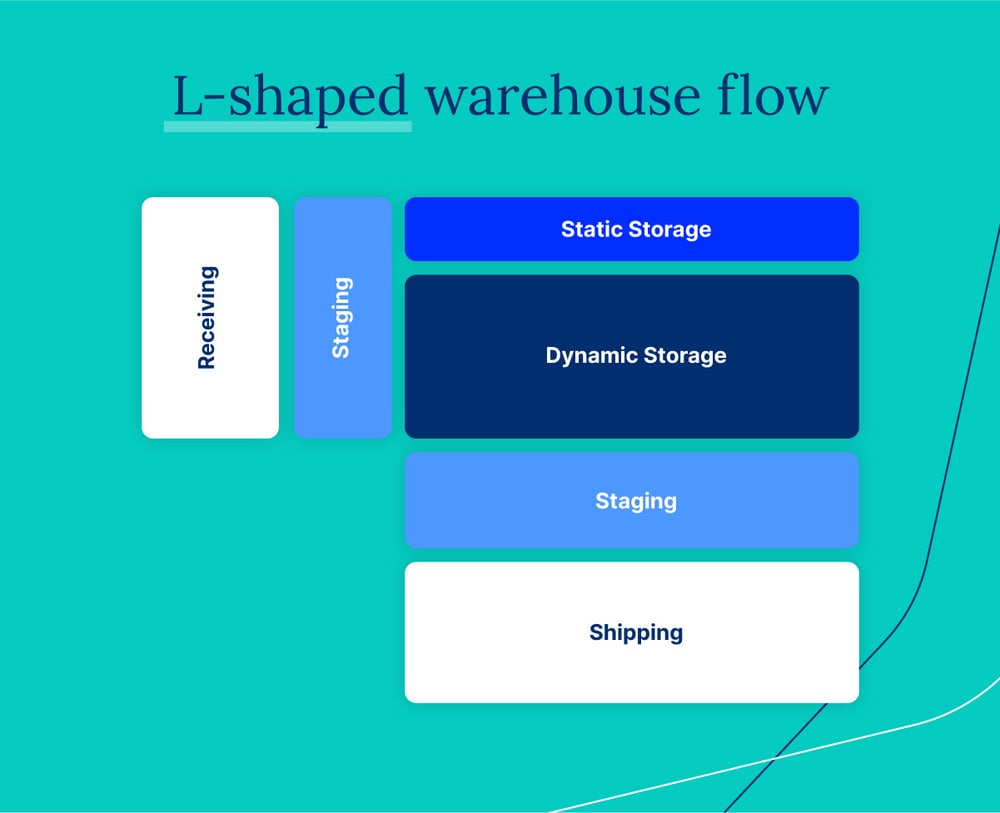
While “L” shaped warehouse layouts are often used to fit an “L” shaped building, that’s not the only benefit. Like the I-shaped flow, the L-shaped flow also reduces back-and-forth movement. It also separates the receiving and shipping areas on different sides of the warehouse to help prevent traffic congestion.
However, the downside of the L-shape is that it requires considerable space to run your operation smoothly, and you’ll still need two sets of loading and unloading equipment.
Best practices of warehouse layout design
Regardless of your chosen warehouse layout, you’ll need to optimize it to ensure efficient operations. Here are some tips you can implement to make the most of your warehousing strategy.
Warehouse mapping
While finalizing the schematics of your warehouse’s design, you should make sure to get the most accurate measurements possible. You’ll also need to label each area of the facility according to its function. Keep in mind that a 2022 survey found the typical company only used 85.6% of its warehouse space.
Each workflow should be established from entry to exit. Once the workflow is designed, you’ll be able to understand how each function connects. After that, you can define the best work processes and train your employees correctly.
Optimizing picking processes
When you adequately plan your picking and packing workflows, you’ll be able to ship the right products to the right customers. There are several picking methods that you can implement to improve your processes.
- Batch picking consists of picking similar orders in batches, all at once. This method is faster than picking one order at a time, and it allows you to fulfill similar orders that include the same SKUs.
- Zone picking is when pickers are assigned specific zones and only pick orders from that area. Zone picking is commonly performed one at a time. If an order needs products that are outside a specific zone, a conveyor belt is often used.
- Wave picking is helpful for warehouses with more significant volumes of products with many SKUs, and combines batch and zone picking. In this method, the picker has to stay within the zone assigned to them, and they are able to pick multiple orders simultaneously.
- Discrete picking is often used in small businesses with fewer SKUs. Whenever an order is received, the picker retrieves all items for the order from different zones of the warehouse. This is time-consuming because pickers are only able to process one order at a time.
As always, you should select the picking strategy that best suits your business and your warehouse. Whatever method you choose, you should focus on maintaining high picking accuracy to reduce the risk of returns.
Ideally, it’s best to have picking areas close to storage areas — which can dramatically reduce the time spent to select ordered items. To increase the efficiency of the picking process, you can also install conveyors.
Improving warehouse accessibility
It’s crucial to place all necessary tools and equipment in spots that are easily accessible to your warehouse workers. There also needs to be enough space for equipment and staff to move freely along designated paths. This speeds up the order fulfillment process to deliver more quickly to customers.
Streamlining the shipping process
The shipping area is where final packing and preparation for shipping take place. Ideally, you want to keep this area separate from other spaces to avoid mixups. It should also be laid out so that staff doesn’t backtrack to complete steps in the process.
Keep best-selling products near shipping areas and products that don’t sell as well farther away. This helps minimize travel picking time and can be accomplished most easily with L- and U-shaped layouts.
Testing and collecting feedback
After finalizing your layout and warehouse flow, you should make sure to run tests and confirm that everything flows smoothly. Equipment like forklifts and conveyors should also be tested.
Allow the employees who will be handling the equipment to test it out and take their feedback into account. Since your picking team will constantly move around the warehouse, you should also work with them to optimize routes for faster fulfillment and less confusion.
You can optimize your strategy and determine the best possible configuration and processes based on feedback and test results.
Final step: Choosing a warehouse management system
Once you decide on your warehouse’s layout and flow, it’s time to choose your warehouse management system. You’d be surprised how much smoother your day-to-day operations and order fulfillment can become with the right management system.
A warehouse management system gives you a real-time view of your inventory’s performance and helps you significantly optimize your warehouse. In fact, 77% of organizations consider warehouse automation systems a crucial part of maximizing performance.
If you’re interested in implementing a warehouse automation system for your business, contact the Cin7 experts to learn more about how we can help.
Frequently Asked Questions
What is the most common warehouse layout?
The most common warehouse layout is the U-shaped warehouse. This shape is popular because it is easy to replicate and has a simple setup.
The U-shape also helps avoid bottlenecks by keeping shipping and receiving on opposite sides of the same end of the building while storage is in the middle.
What is the best warehouse shape?
The best warehouse design for your business really depends on a number of factors. Budget, inventory size and type, number of orders, safety requirements, and your warehouse space can all affect which is best for you.
U-shaped warehouses are good general designs that work for a large number of situations. I-shapes are great for large order volumes or the use of conveyor belts. L-shapes help reduce back-and-forth movement, which is helpful for large products and controlling traffic flow.
More from the blog
View All Posts
How to ensure a successful WMS implementation
Read More
Cin7 Leads the Way: Groundbreaking Updates and Innovations in Inventory Management
Read More