Transforming manufacturing with Demand-Driven MRP: A complete guide
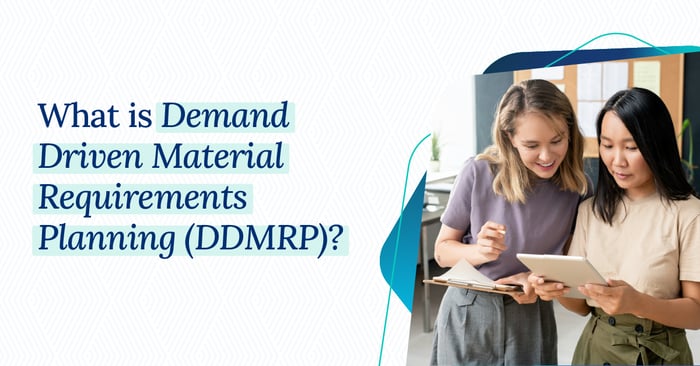
Since its introduction in the 1960s, companies worldwide have relied on materials requirements planning (MRP) to determine the number of materials, parts, or components they need to assemble each end item in production.
However, today’s manufacturing environment has evolved dramatically from those early days. The modern landscape is characterized by volatility, uncertainty, complexity, and ambiguity (VUCA), which makes it challenging to create accurate demand forecasts.
Traditional MRP systems, which rely heavily on forecast accuracy, often struggle in such environments, leading to problems such as overstocking, understocking, and inefficient production planning. These issues can result in higher inventory carrying costs, lower customer satisfaction, and reduced profitability.
To navigate this new dynamic environment, manufacturers are increasingly turning to a more flexible and responsive approach to manufacturing planning and execution known as Demand Driven Material Requirements Planning (DDMRP).
Here’s what you need to know about DDMRP, including the primary benefits of implementing it in your organization.
What is Demand Driven Material Requirements Planning (DDMRP)?
Demand Driven Material Requirements Planning (DDMRP) is an innovative approach to material control and replenishment that extends the principles of traditional MRP systems to better suit today’s fast-changing market conditions. Unlike conventional MRP systems — which rely heavily on forecast-driven planning — DDMRP emphasizes a demand-driven approach, which enables greater responsiveness and flexibility to changes in the manufacturing environment.
At the heart of DDMRP is the strategic placement and management of “decoupling points.”These are specific inventory buffers positioned at critical stages in the supply chain to help manage variability and maintain the smooth flow of materials.
Placing decoupling points strategically enables manufacturers to isolate disruptions like supply delays or demand fluctuation from impacting other parts of the supply chain. This helps avoid the “bullwhip effect,” where small changes in demand can cause increasingly larger fluctuations further up the supply chain.
According to Carol Ptak and Chad Smith (2011), the original creators of DDRM, this methodology equips companies to better handle variability in supply and demand. It allows them to manage inventory levels more effectively while maintaining the same or even improving customer service levels.
Key components of DDMRP
Demand-driven MRP comprises five sequential components or phases. The first three define how the DDMRP model is uniquely tailored to fit your organization’s needs and circumstances, while the last two define its execution or day-to-day operation.
- Strategic Inventory Positioning: This phase involves determining where to position decoupling points in your supply chain. The goal is to place inventory buffers at locations where they will have the most significant impact in mitigating variability and ensuring a smooth production flow.
- Buffer Profiles and Levels: This phase involves determining the amount of protection (i.e the amount of inventory buffer) to put at each of the established decoupling points.
- Dynamic Adjustments: This component defines how the level of protection at each decoupling point flexes up or down in response to changing conditions, such as shifts in market demand or variations in operating parameters. This flexibility ensures that inventory levels are consistently aligned with the current conditions of the business environment.
- Demand-Driven Planning: At this stage, the system calculates supply requirements (using a net flow equation) and generates supply orders — such as purchase, manufacturing, and stock transfer orders.
- Visible and Collaborative Execution: This is the operational phase where the DDMRP system manages open supply orders. It involves executing the demand-driven plan while maintaining clear visibility across the supply chain. Collaboration among all stakeholders is emphasized to ensure demand signals are correctly interpreted and acted upon in a timely manner.
Benefits of implementing DDMRP in manufacturing
Now that we know what demand planning and its key components are, let’s look at some of its main benefits when implemented.
Enhanced inventory management
As we mentioned earlier, one of the drawbacks of traditional MRP is that it struggles with balancing inventory levels in dynamic environments, leading to either excess inventory, which ties up capital and increases carrying costs, or stockouts, which can disrupt production and lead to missed sales opportunities. DDMRP addresses these challenges by aligning supply more closely with actual demand.
By strategically positioning decoupling points and dynamically adjusting buffer levels at these points, DDMRP ensures that inventory is available where and when it is needed, without overproducing or overstocking. This approach reduces the risk of holding excess inventory, which can quickly become obsolete in fast-changing markets, and minimizes the likelihood of stockouts, ensuring that production can continue uninterrupted.
Improved responsiveness to market changes
DDMRP leverages real-time demand signals to drive planning and production decisions. That enables manufacturers to respond more swiftly and effectively to market fluctuations. Moreover, the enhanced visibility and transparency provided by DDMRP fosters better coordination across the supply chain.
Reduced lead times
DDMRP can reduce manufacturing lead times through its strategic use of decoupling points and dynamic inventory buffers. Positioning these buffers at critical stages in the supply chain effectively absorbs variability and ensures a smoother flow of materials and components. This reduces the need for last-minute adjustments and rush orders, which can be costly and time-consuming.
Furthermore, by aligning production schedules more closely with real-time demand, DDMRP minimizes the waiting time between different stages of the manufacturing process. This results in a more continuous and efficient workflow, allowing manufacturers to fulfill customer orders more quickly.
DDMRP implementation challenges and how to overcome them
While DDMRP offers many benefits, implementing it can present several challenges for manufacturers. Here are some of the most common hurdles and strategies for overcoming them:
System integration complexities
Integrating DDMRP with existing enterprise resource planning systems (ERP) or inventory software and other relevant systems or software can be complex, particularly if your current systems are outdated or not designed to support DDMRP functionalities.
One way to overcome this challenge is to collaborate with IT specialists and DDMRP experts to develop a detailed integration plan that includes a comprehensive assessment of current systems, required modifications, and integration points.
You can also use middleware solutions to bridge any compatibility gaps between DDMRP and your existing systems.
Resistance to change
Transitioning to DDMRP often involves significant changes in processes, roles, and responsibilities. If employees are already accustomed to MRP, they may be resistant to the transition, due to concerns about job security or discomfort with new practices.
To overcome this challenge, develop a clear communication strategy that outlines how DDMRP will positively impact the company and its staff. Engage the employees and other relevant stakeholders early in the process to build buy-in and support for the transition.
Lack of expertise
Lack of knowledge about DDMRP principles, methodologies, and tools can lead to improper implementation, underutilization of the system, and failure to achieve the desired results.
So to avoid this hurdle, invest in training and upskilling your current workforce to build internal DDMRP expertise. This could include workshops, online courses, and certification programs. Additionally, consider hiring external consultants or partnering with DDMRP-certified professionals who can guide the implementation process, provide expertise insights, and mentor your internal team.
Make sure your employees also have access to support resources and documentation to assist them in adapting to the new system.
Cost of implementation
Implementing DDMRP usually requires substantial upfront investments in new software, training, and consulting services. For some organizations, these costs may be a big barrier to adoption and implementation.
The key to overcoming this barrier is to focus on the long-term return on investment (ROI) of DDMRP. Emphasize the potential cost savings and efficiency gains — such as reduced inventory expenses, shorter lead times, and enhanced customer satisfaction — all of which can contribute to improved profitability for your business.
Additionally, to manage upfront costs, you can also consider a phased implementation approach. This strategy allows you to spread the costs over time, making the transition more manageable and less financially burdensome.
Demand-Driven MMR case studies
Several companies have implemented DDMRP to resounding success. Here are a few standout examples.
- Jamestown Container Companies — Implementing DDMRP reduced inventory and lead times by 60% and 70% respectively while increasing operating profit by a staggering 300%.
- ABI Attachments — Adopting DDMRP helped the company decrease on-hand inventory by 18% and increase sales by 12% year-on-year while maintaining service levels at a stable 94%.
- Amore Pacific – DDMRP helped the company lower its raw materials inventory by 20% while increasing the service level to 99%.
Summary
The original MRP system was developed for a time when businesses operated in relatively stable environments with predictable demand patterns and shorter supply chains.
However, as market conditions have evolved, these forecast-based systems have proven less effective, often resulting in excess inventory, frequent stockouts, and lengthy lead times.
DDMRP offers an effective solution to these challenges by focusing on actual demand. It uses strategically positioned decoupling points and real-time demand signals to guide replenishment and production decisions.
This approach helps you to better manage variability in demand and supply, optimize inventory levels, and improve overall manufacturing efficiency.
Using Cin7 to support DDMRP implementation
Cin7, a leading inventory management solution, can be an invaluable partner in implementing DDMRP in your organization.
Cin7 offers powerful features such as real-time inventory tracking and advanced analytics and reporting. With Cin7, you can streamline your inventory processes, improve order accuracy, and gain real-time visibility across your entire supply chain.
Schedule a demo today to see how Cin7’s inventory management solutions can help you leverage DDMRP and drive your business toward greater success.
More from the blog
View All Posts
What To Do When Products Go Viral
Read More
Demand planning: What is it? Principles and importance
Read More