
Can you believe we live in a world where robots and humans work together? It sounds like the plot of a science fiction movie, but it’s actually happening. From large corporations to small businesses, the future of warehouses is automated.
Warehouse automation has shown stunning growth since the 2010s, as projections indicate the market could be worth $41 billion by 2027. We can attribute most of this growth to the e-commerce industry, and projections indicate those sales will reach $8.1 trillion by 2026.
But it’s not just e-commerce retailers who use warehouse automation. BMW, for example, optimizes its warehouse processes with Automated Guided Vehicles (AGVs) and inventory management software. Walmart recently invested in Symbiotic, a robotics and warehouse automation company, and plans to automate warehouses and retail locations over the next few years.
Warehouse automation uses automated technology to optimize processes, improve efficiency, gather data for insights, and minimize repetitive tasks for workers. More than robots, warehouse automation is made possible by automation software, Internet of Things (IoT) devices, automated vehicles, and even the blockchain.
As automated warehouse systems become the norm, businesses must stay ahead of market trends and technological developments. Basic knowledge of warehouse automation can help business leaders make informed decisions. In this article, you’ll learn the:
- Types of warehouse automation available
- Benefits of warehouse automation in business
- Challenges of warehouse automation
- Top warehouse automation trends
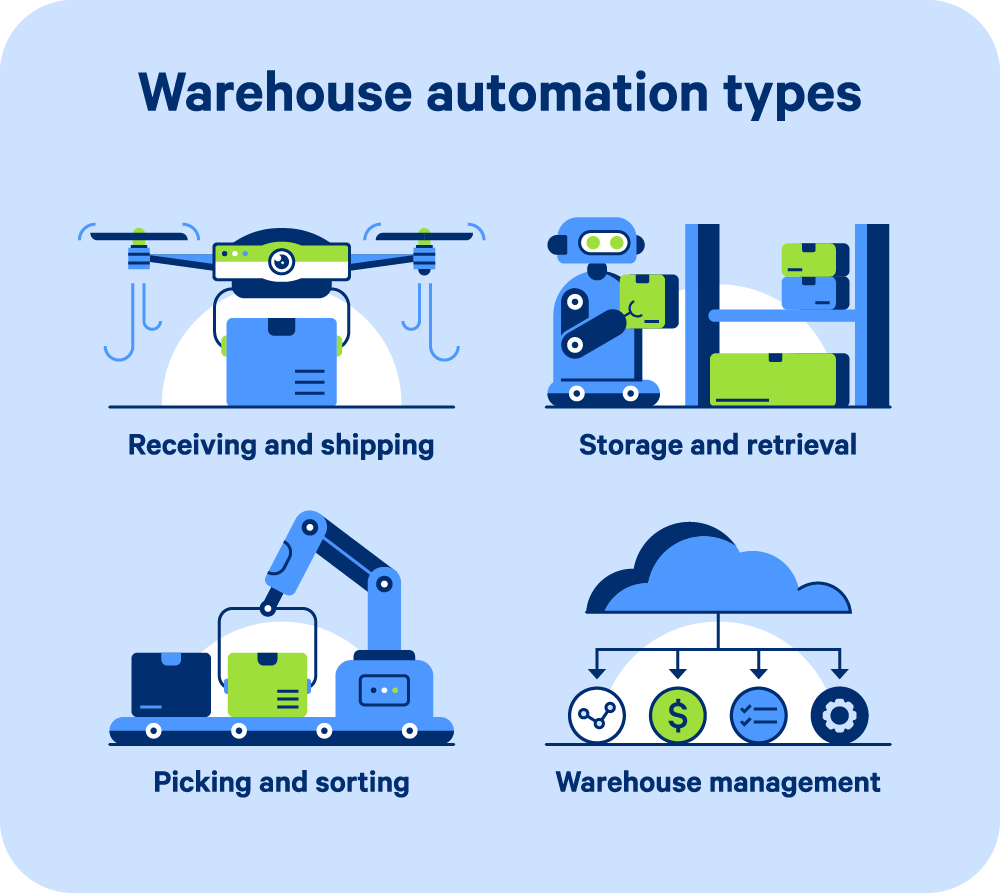
4 types of warehouse automation
Warehouse automation technology comes in many forms that you can combine in simple or complex ways. This spectrum of complexity spans from basic conveyor systems to advanced robotics integrated with AI technology. We want to provide a list of available methods by explaining the types of warehouse automation technology available in today’s market.
Receiving and shipping
Automation can’t change fuel prices, but it can improve the efficiency of outbound shipping and inbound receiving processes. These efficiencies can save businesses money and improve customer satisfaction by minimizing touchpoints and decreasing the Total Cost of Ownership (TCO). Here are a few leading methods in automating logistics:
- Automated inbound receiving technology: This technology combines automated versions of conveyors, scanners, labelers, and order verification to simplify inbound receiving tasks. A complex automated receiving system can move, identify, label, and verify all goods against the purchase order without requiring human labor.
- Automated outbound shipping technology: Outbound shipping automation can detect important labels (including human writing), detect damage, measure items for shipment, and ensure order accuracy. The shipment information is made available immediately through an integrated warehouse management system (WMS).
- Drones and delivery robots: Drones and delivery robots are changing last-mile deliveries. Customers can receive goods faster and without needing human labor in the shipping process.
Storage and retrieval
The physical act of storing and retrieving goods can be repetitive and dangerous for humans. Offloading these tasks can improve productivity while minimizing safety concerns. Goods-to-person (GTP) technologies can improve accuracy and efficiency when storing or retrieving goods. Be it for manufacturing or order fulfillment.
In one example, Kubota Canada recovered 83% of their floor space by using Vertical Lift Modules (VLM) and horizontal carousels in their distribution center. The benefits of their reduced storage were twofold: Their warehouse became more efficient, and they used the newly freed space for profit.
Available solutions are detailed below.
- Automatic storage and retrieval systems (AS/RS): AS/RS systems combine robotics and computer systems to augment storage and retrieval in a warehouse. The optimization of storage can increase the density of goods and maximize available storage space. The AS/RS category has many products, including vertical storage systems, horizontal carousel modules, and VLMs.
- Automated guided vehicles (AGV): These vehicles can carry loads and handle materials with little human input or operation. Companies will primarily use them within warehouses, distribution centers, assembly lines, and manufacturing facilities. In general, their movement is limited to fixed paths and rail systems.
- Autonomous mobile robots (AMR): AMRs are similar to AGVs, except that robots have the advantage of dynamic mobility. AMRs use advanced sensors and AI processing to adapt and redefine their paths in a warehouse setting. For this reason, they can work safely near humans.
- Exoskeletons: Exoskeletons are machine suits that augment a human’s capacity for work. They currently address gaps in automation, where a human is required to perform physically demanding tasks unsuitable for robots. Exoskeletons use sophisticated automation and sensors to improve a worker’s ability to lift and move heavy objects.
Picking and sorting
Picking and sorting costs can add up in the long run. According to the Georgia Institute of Technology, about 63% of a warehouse’s operating costs can trace back to order picking. Combining automated picking and sorting technology can decrease costs and increase efficiency.
Consider the following examples of picking and sorting automation:
-
- Collaborative mobile robots: Companies may program these robots, sometimes called “cobots,” to assist warehouse workers, and quickly augment manufacturing and warehouse processes such as assembly, handling of materials, and quality assurance.
- Automated sortation systems: These systems combine scanners with product handling technology such as conveyor belts. They can be fully or semi-robotic. Certain systems can apply labels, wrap packages, and more. Depending on the items and system, sorting capacity can range from 20 sorts per minute to 833 sorts per minute.
- Automated picking systems: This category encompasses a range of robotic and semi-robotic systems capable of picking, organizing, routing, and shipping. A high-speed system can accurately pick up to 450 items per minute.
- Pick-to-light: This automated picking system functions as a guide for human pickers. Pick-to-light uses LEDs and other lights to show exact pick locations. They can reduce overhead costs by minimizing inaccuracies, streamlining the picking process, and reducing cognitive load for workers.
- Voice picking and voice tasking: Just like the name suggests, these systems use voice recognition to augment the picking process for human workers. Workers come equipped with headsets that relay picking information to them hands-free. Workers can then respond verbally or communicate with the program using scanners.
Warehouse management
Warehouse management systems (WMS) are the heart of an automated warehouse system. For example, robotic systems communicate with these systems as they receive, store, pick, sort, and ship goods within the warehouse. Warehouse management software can also integrate with third-party logistics (3PL) solutions and automate manual processes.
These systems can optimize warehouse storage space, calculate inventory, schedule purchase orders and deliveries, manage product demand fluctuations and returns, and integrate with 3PL.
WMS offer a range of capabilities using automation. Some of the main capabilities of WMS include:
-
- Cloud-based inventory management: Cloud-based systems are integral for modern warehouse logistics. Real-time management allows for automated inventory adjustments in response to fluctuating demand and availability. Their cloud-based functionality supports integration with robotic and automated warehouse systems.
- Reports and forecasting: WMS simplify forecasting by automatically pulling data from all available sources. These systems use automation to compile and aggregate data to streamline reporting and forecasting. You can optimize order fulfillment by using this quick and accurate data pulled in real-time from all warehouse departments.
- Order management and fulfillment: Automated order management systems can speed up fulfillment, replenishment, purchasing, and sales orders. Using real-time information, the WMS can send POs automatically when inventory reaches a certain volume. Branch transfers can automatically occur as determined by pre-set conditions.
- Built-in Electronic Data Interchange (EDI): Rather than using a third-party solution, WMS can support built-in EDI. This allows the automation of workflows, including order download, shipping, and the processing of invoices. Manual data entry can also be reduced by rule-based automation.
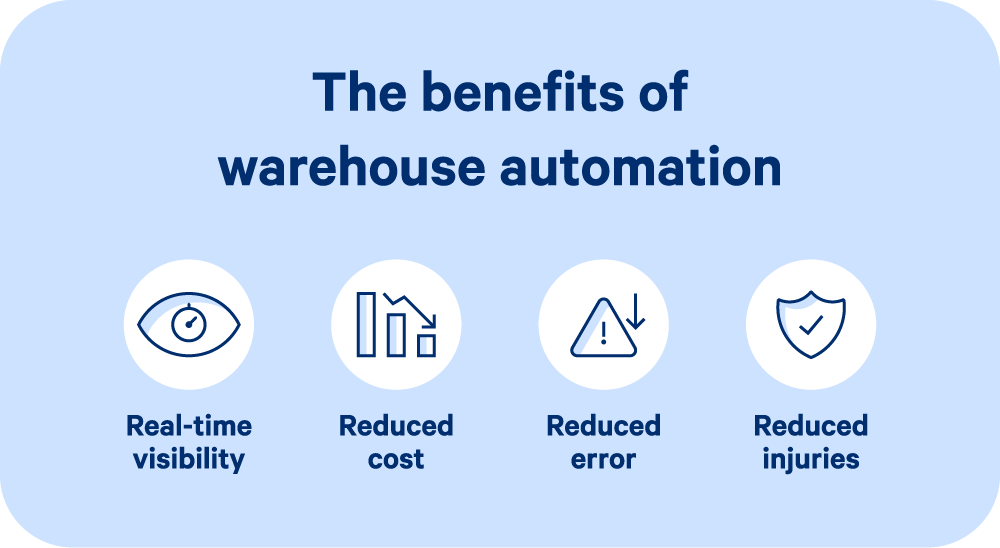
4 benefits of warehouse automation
Every business should consider how automation can benefit their particular use case. No two businesses are the same, so any automation must be onboarded with deep consideration. The warehousing industry has many pain points that automation can alleviate. Here are a few of those benefits.
1. Real-time visibility
One of the immediate benefits of warehouse automation is real-time inventory visibility. Cloud data supports visibility from warehouse storage to distribution and everything in between. A prime example is e-commerce, where response times and customer satisfaction are key to a successful business.
Knowing exact stock levels at all times allows businesses to:
- Accurately forecast demand
- Keep optimal stock levels
- Make quick decisions
- Create data-informed strategies
- Keep customers happy by avoiding stockouts and backorders
2. Reduced cost
Warehouse automation can reduce costs associated with just about every process and procedure. For example, optimizing storage and freeing up floor space creates new revenue opportunities. Up to 80% of basic shelving can be considered wasted space. Automation makes it possible to reduce this waste and recoup those costs. Labor productivity increases as humans work more efficiently alongside their automated counterparts.
Warehouse automation reduces costs by improving:
- Human labor and manual processes
- Reporting and forecasting
- Storage capacity
- Warehouse scalability
3. Reduced error
Automated systems reduce error significantly in comparison to non-automated systems. Human error is an inevitable factor in manual processes. According to a study by the University of Hawaii, manually updating inventory spreadsheets can lead to error rates as high as 86%.
Automated systems are not prepared to fully automate all aspects of a warehouse. But automation can greatly reduce error in certain areas. For example, automated storage and retrieval systems can increase the accuracy of associated tasks by up to 99.99%.
Overall, warehouse automation can reduce errors by:
- Minimizing the need for manual input
- Augmenting manual input with rule-based automation
- Reducing worker fatigue
- Supporting proactive decision-making with real-time data
4. Reduced risk of injury
Fatal work injuries in transportation and warehousing are some of the highest in any industry. There were 976 fatal workplace injuries in transportation and warehousing in 2021. Construction was number one, with just 10 more fatalities per year.
A study by the University of Pittsburgh showed that work-related injury rates were reduced due to the introduction of robotics. Other data in the study indicated a 4% decline in “physical job intensity” and a 5% drop in disability. Whether it’s picking or inventory management, automated warehouse systems can reduce manual work requirements and the associated fatigue. Workers can stay focused and avoid injury in a warehouse setting by reducing fatigue and cognitive load.
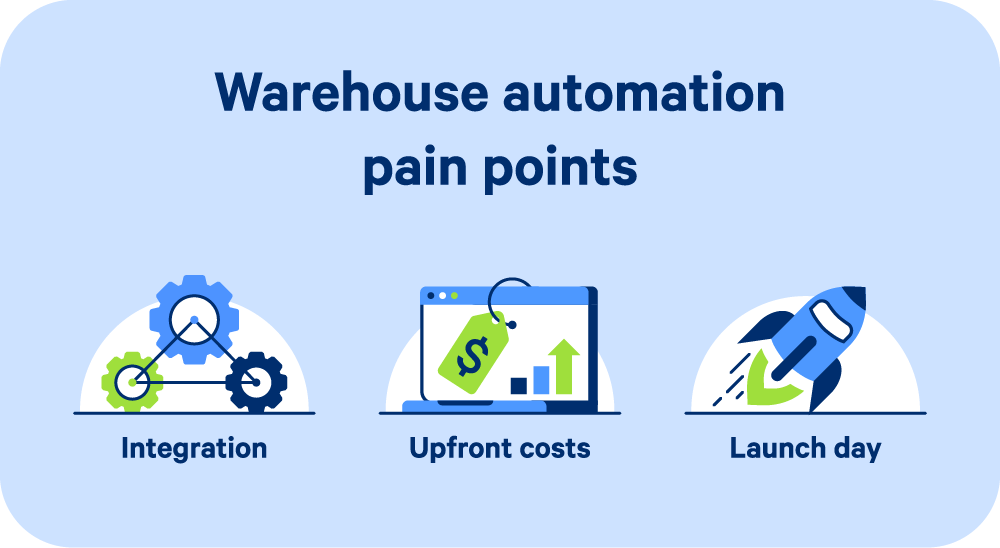
3 challenges of warehouse automation
With significant benefits come challenges. Many of these challenges occur in the early phases of automating a warehouse. Take stock of which challenges will impact your business the most so you can plan to address them.
Create an implementation committee to oversee the automating project. They can keep stakeholders informed, organize efforts, ensure regulatory compliance, and support a smooth transition toward automation.
We’ve outlined some of the main challenges associated with introducing warehouse automation below.
1. Integration
Integrating any new systems or technologies can be challenging, especially when those systems involve a lot of essential customer data. Furthermore, new technologies require training and a period of adjustment for teams.
For example, a business may want to stick with its enterprise resource planning (ERP) system if it already has a warehouse management system (WMS) feature. This feature may work now, but switching to a dedicated WMS is important for scaling with increasing complexity, and it will have more robust functionality than the ERP system’s WMS feature.
Small and medium-sized businesses can implement an inventory and warehouse management system much cheaper and faster than a traditional ERP. This solution combines inventory management system (IMS) and WMS technology with automation that is built to scale. Integration is important, and choosing an all-in-one solution can save time while reducing startup costs.
There is no simple solution when automating a process that involves many steps. Depending on the complexity of your warehouse automation, it can take 4-12 weeks of onboarding. During this time, your task force must pay close attention and prepare to remediate any issues.
2. Upfront costs
While warehouse automation pays off in the long run, the upfront costs can be significant. Average costs can range from $15,000 to more than $200,000 depending on the size and complexity of your operations. We’ve provided some averages for you to consider regarding your warehouse automation needs:
- AS/RS systems have varied costs, ranging from $70,000 for a Vertical Carousel Module and $1.5 million for Robotic Cube Storage.
- Robotic arms alone can cost anywhere from $50,000 to $80,000.
These solutions can be worth the investment when warehouse labor takes about 65% of most operating budgets. Budgets should plan for all upfront costs, such as the number of users, required peripheral devices, and installation costs.
3. Launch day
Some stress is normal leading up to a new system launch. Did we set it up right? Are there issues we aren’t seeing? Growing pains are common for any business that bravely enters a new territory. Organize your launch days thoroughly to mitigate any issues during this exciting phase.
Remember these best practices:
- Plan to monitor, test, validate, and potentially abort the launch.
- Budget for extra resources required during the launch phase.
- Communicate with vendors and make sure they are available to supervise during the launch process.
Establish automation committees well ahead of launch day. The committee can establish key metrics for validating processes and potentially aborting the launch. A dedicated party can communicate with multiple stakeholders and ensure everybody has the resources they need for a successful launch.
5 warehouse automation trends
The warehouse automation market continues to grow, potentially exceeding $69 billion by 2025. Warehousing is more predictable than other industries, like construction, which makes it a prime environment for automation. Here are some warehouse automation trends we’re seeing right now.
- Automated guided vehicles: The AGV sector is predicted to reach $9.18 billion by 2030. Autonomous vehicles are restricted now but have the potential to be highway ready in the future.
- Additive manufacturing: This application of 3D printing creates spare parts (and more) in an industrial setting. The market was valued at $16 billion in 2022 and is predicted to reach $94 billion by 2032.
- Blockchain: This technology creates a decentralized record of transactions that all partners in a supply chain can access. These digital ledgers can improve visibility, accuracy, and accessibility. The adoption rate for blockchain technology could potentially reach 45% percent by 2030.
- Internet of Things (IoT): These “things” can relay valuable data that leads to powerful business insights. For example, businesses can use IoT data for predictive maintenance, which reduces breakdowns by 70%.
- Cloud solutions: The reliability and scalability of cloud technologies show no signs of slowing down. The cloud automation market is predicted to reach $480 billion by 2030.
How do you automate warehouse processes?
Warehouse processes can be easily automated when they are repeatable and somewhat predictable. Warehouse automation technology continues to advance in ways that make it increasingly flexible, adaptable, and scalable. Whether you consider a robotic picking system or a cloud-based order fulfillment solution, it all comes down to your business needs.
A warehouse management system is one of the key components of an automated warehouse. No sophisticated system can rely on manually updated spreadsheets — you need a reliable WMS to connect all your order, inventory, shipping, and accounting workflows.
Take your business to the next level with Cin7 Inventory and Warehouse Management Software solutions.
More from the blog
View All Posts
Complete Guide to Inventory Management: Types, Efficiency and More
Read More
Maximize the Cost-Saving Benefits of Inventory Management Software With Cin7
Read More