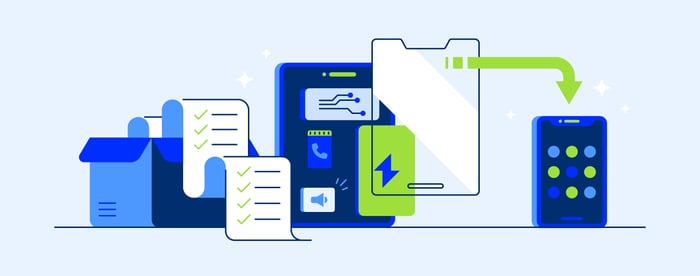
Ever been halfway through making a pizza and realize you forgot to buy cheese? Or started building a treehouse only to find out you don’t have a hammer?
Believe it or not, manufacturers plan their production process in a similar way. Just like how we jot down all the ingredients we need to make a pizza, manufacturers track everything they need to create a product. But in manufacturing, the stakes are much higher. So, they don’t just rely on iPhone notes. Instead, they use a special, standardized document called a bill of materials.
A bill of materials (BOM) is a list of all the materials and components required to build a finished product. You can think of it like a recipe for a product that lists all the needed ingredients and their quantities.
A well-structured BOM can help companies in various ways, including:
- Planning purchases of raw materials
- Estimating material costs
- Gaining inventory control
- Tracking and planning material requirements
- Maintaining accurate records
- Ensuring supply robustness and cutting waste
Creating a BOM is the first step in getting a product into production. Without a BOM, it can be difficult to track profits, communicate with the shop floor, or ensure that the right materials are on hand when needed. Taking the time to create a well-structured BOM can improve your efficiency, reduce costs, and ensure that your products get built to the highest standards.
Stay with us as we explore the different types of BOMs, how to make a BOM, and the essential information to include in them.
Key Takeaways:
- A bill of materials (BOM) encompasses all the materials, components, and information necessary to assemble a product.
- There are multiple types of BOMs, including manufacturing BOMs, engineering BOMs, sales BOMs, production BOMs, and configurable BOMs.
- BOMs are typically displayed in either a single-level view or a multi-level view.
- There are some universal elements you should include in every BOM, like part number, part name, raw materials, quantity, and more.
Types of BOM
Different departments utilize various types of BOMs, each focusing on their specific needs. These BOM types include:
1. Manufacturing bill of materials
A manufacturing bill of materials (MBOM) is a structured list of all parts or items needed to create a complete product. All teams involved in the order cycle will receive the information to ensure all the correct people have visibility into the process.
2. Engineering bill of materials
An engineering bill of materials (EBOM) includes parts designed by the engineering department, typically involving a mechanical or technical drawing of the finished good. It’s common for a product to have multiple EBOMs due to necessary design modifications.
3. Sales bill of materials
A sales bill of materials (SBOM) outlines the product in the sales stage and details each product before its assembly. In this context, the finished product is considered a sales item, not an inventory item.
4. Production bill of materials
A production bill of materials (PBOM) serves as a guide for the components comprising a product. It lists the necessary components and makes adjustments throughout the production process as components become finished products.
5. Configurable bill of materials
A configurable bill of materials (cBOM) is used for products that need specific customer adaptations, such as unique shipping and packaging requirements.
BOM structures
There are two main ways you can present and structure a BOM, and the method you use will likely depend on the complexity of your product. The two structures are:
Single-level bill of materials
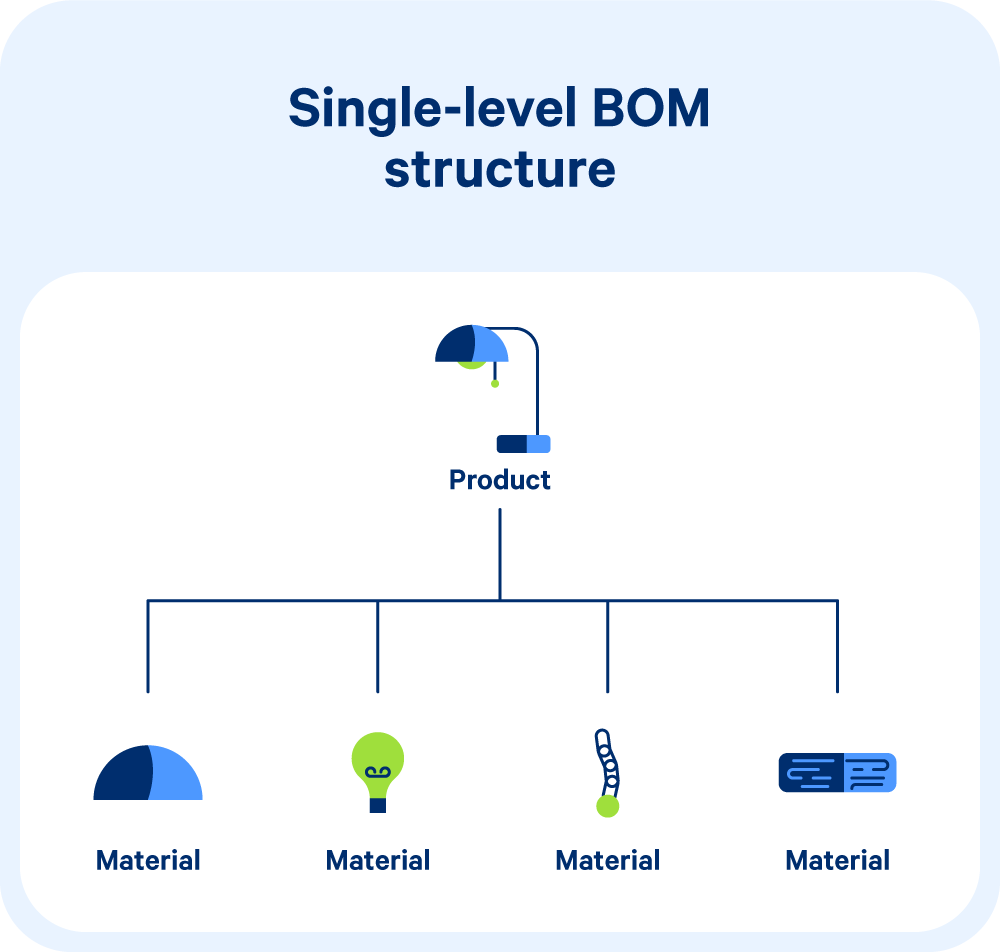
Simpler products with fewer parts and straightforward assembly will often require a single-level bill of materials. It’s not favored for complex products due to its inability to clearly define relationships between parent and child parts or between assemblies and sub-assemblies.
Consequently, if production issues occur, this BOM type lacks the specificity to pinpoint the origin of the problems.
Multi-level bill of materials
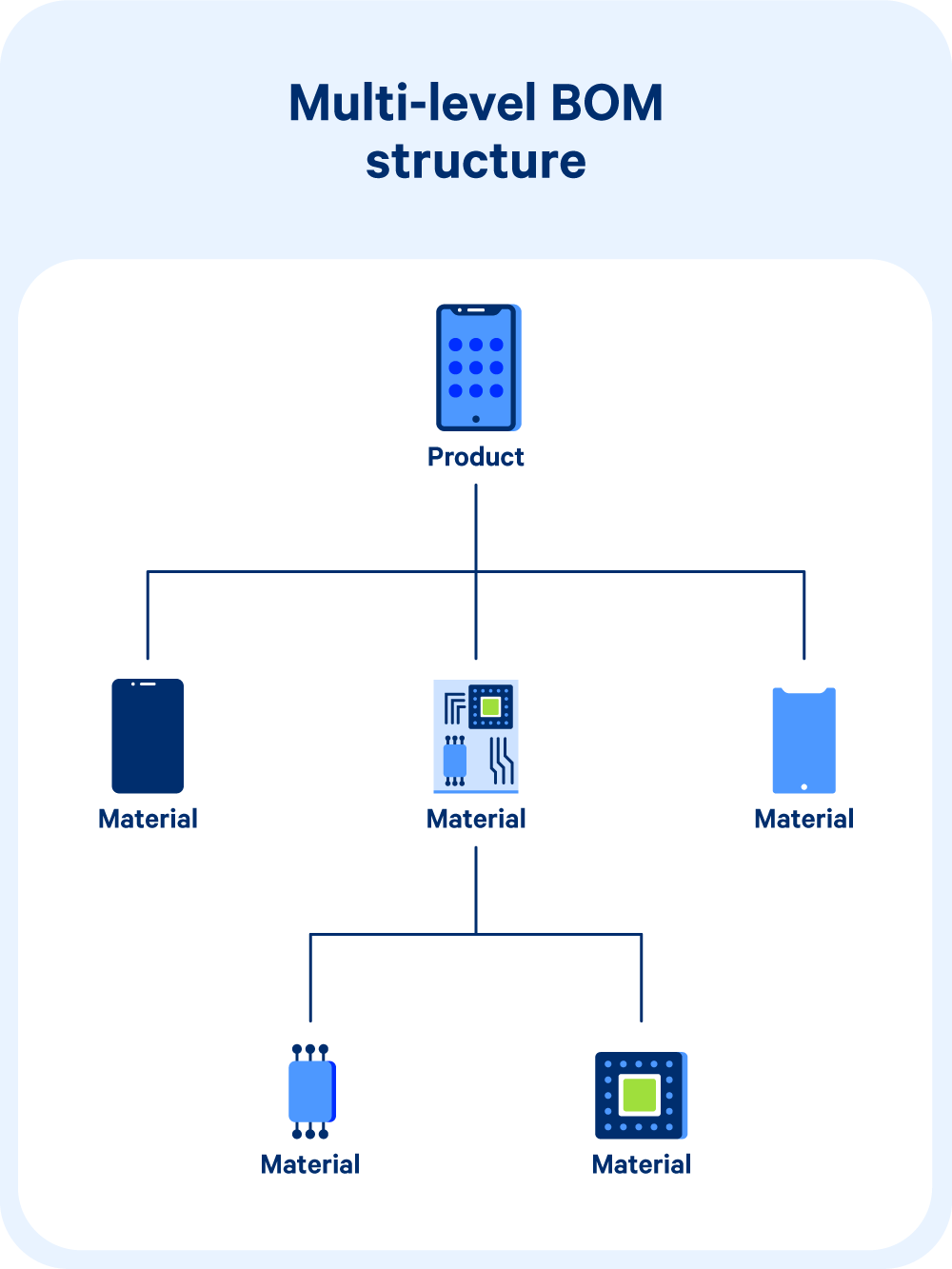
While a multi-level bill of materials requires more time to create than a single-level BOM, it provides superior detail and reliability regarding the product’s parent and child parts. Moreover, multi-level BOMs depict the full relationship between these parts.
As this BOM encapsulates all product-related aspects, its utility extends beyond manufacturing. It can also enhance engineering, design, sales orders, and material management processes.
How to make a bill of materials
After identifying the BOM structure you’ll use, you’re now ready to begin crafting your own. Developing a BOM is a strategic endeavor that needs careful planning to avoid future hiccups. Here are the steps you should take when making your BOM:
1. Decide what you need to include
First, outline what your BOM should include. While it might seem evident, detailing every item — even seemingly unimportant ones — is vital. This avoids any potential omissions during later stages.
2. Collect and assemble information
Assembling the necessary information for your BOM is easier said than done. Therefore, you must find a way to centralize the data. Comprehensive inventory tracking software is the best way to unify information in a single platform.
3. Select editors
To ensure BOM accuracy as items change during production, limit BOM editing to a select few within your organization. Modifications will likely need to be made to the BOM during the production process, so it’s better to only let a select few dictate these changes.
4. Choose a BOM structure
Next, choose your display method—single-level or multi-level. For simpler products, a single-level BOM suffices. For more intricate items, consider a multi-level BOM.
For instance, a bike might seem composed only of wheels, a frame, handlebars, and a seat. However, multiple components go into making frames and wheels—spokes, tubing, etc. — which also need tracking.
5. Create the BOM
With all BOM specifics decided, it’s time to create it. Certain information always requires inclusion, regardless of the product. We’ll dive further into these essential details next.
What does a bill of materials include?
The BOM works to ensure the product is built correctly, so you should always include the following pieces of product data in the BOM record:
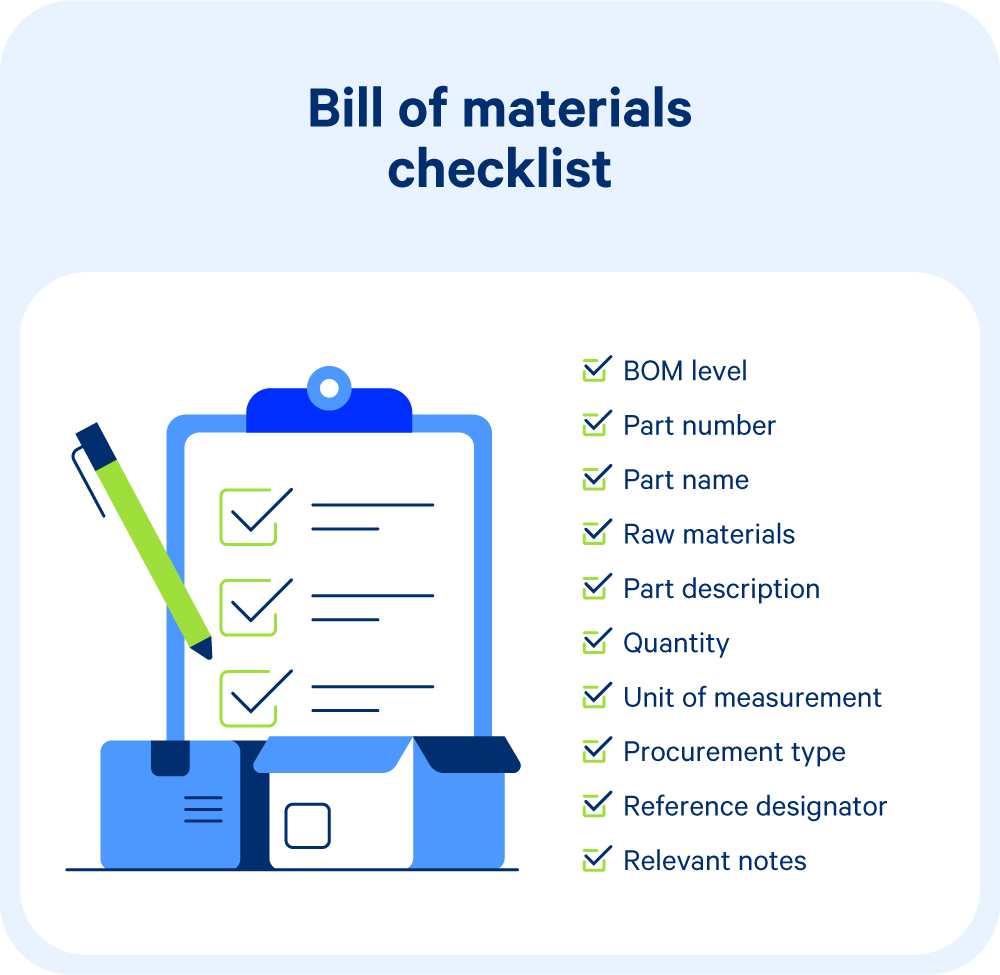
- BOM Level: This is the rank or number for all your parts. The BOM level keeps tabs on every part of your BOM, whether single- or multi-level.
- Part Number: This is the unique part number assigned to each item, making it easy to reference and track all parts.
- Part name: This is the unique name of all the parts in the product.
- Raw materials: This specifies the precise quality or raw material type required for the manufacturing process.
- Part description: A detailed description of each part helps distinguish between similar parts.
- Quantity: The number of parts utilized in each assembly or subassembly must be documented to direct purchasing and manufacturing activities.
- Unit of measurement: This illustrates what unit the part will be measured in.
- Procurement type: Document each part you purchase or make (i.e., off-the-shelf or made-to-specification) to develop efficiencies in planning, manufacturing, and procurement activities.
- Reference designators: In case your product includes printed circuit board assemblies (PCBAs), incorporating reference designators within your BOM is critical to illustrate where the part fits on the board.
- Relevant notes: Ensure that additional relevant notes are captured to keep all parties who interact with your BOM informed. Accurate documentation within the BOM aims to save time and prevent confusion in the future.
Tips for creating an impactful BOM
A BOM’s efficiency relies on more than the sum of its parts. Regardless of its complexities and what it includes, the following four principles lay the foundation for creating an efficient BOM.
1. Tailor your BOM to project needs
Before creating a BOM, discern the vital details and design the BOM to meet these specifications. Tailor your BOM to suit the unique demands of the project or build.
2. Include enough detail
Include comprehensive information to ensure your BOM is as precise, accurate, and as detailed as possible. Although some details may seem redundant, there’s a general guideline to follow:, The more detail, the better.
3. Double-check for accuracy
Before uploading or forwarding your BOM, verify that it contains all necessary information and that the data is correct. Small errors can have significant repercussions, hence the need to double-check the details and ensure their accuracy.
H3: 4. Limit access
Restrict the number of individuals who can edit the BOM. While other members of the organization can access and utilize the BOM, prevent them from making modifications. This safeguard helps mitigate potential human error.
Frequently asked questions (FAQ)
Still wondering about what a BOM is and how to create your own? Look no further. Here are some of the most common questions and answers about BOMs and the process of creating one.
What is the meaning of a bill of materials?
A bill of materials is an exhaustive list of materials required to produce a product, along with any additional instructions and information pertinent to the production process.
What is a bill of materials example?
Consider a pizzeria tasked with making 100 pizzas. The BOM would encompass everything required to make the pizzas, such as dough, pizza sauce, and cheese, as well as resources for cooking the pizzas, like pans and ovens. A multi-level BOM would go even further to include child ingredients, like the water, flour, and yeast that are used to create the dough.
Does a bill of materials include prices?
A BOM typically includes the price of each material or component.
Does a bill of materials include labor?
A BOM typically does not include labor. Rather, the BOM includes components, parts, and prices. Labor is reported separately.
What is the purpose of a bill of materials?
BOMs are essential tools in eliminating problems in a company that runs lean and continuous improvement processes. They help reduce errors like ordering the wrong part, wrong quantities, or similar issues that lead to costly downtime and production delays.
By automating your BOM with an inventory management solution, you can get up-to-date demand forecasting and the ability to modify the list easily. This will prepare you for anything that arises during the manufacturing process.
Create BOMs with ease with Cin7.
More from the blog
View All Posts
Manufacturer Part Number: Benefits and Applications
Read More
Best Practices for Managing Sales Channels and How Cin7 Can Help
Read More