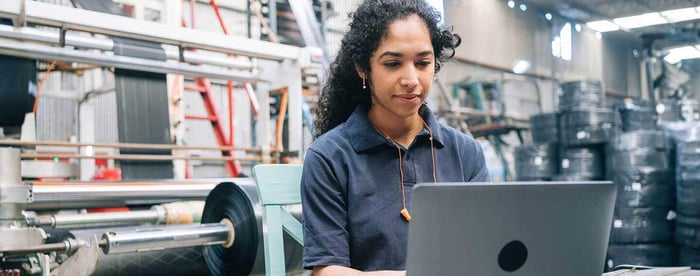
MRP software isn’t a new innovation. Believe it or not, MRP software was used in the 60s when Joseph Orlicky developed it to help growing businesses like Black & Decker.
While its beginnings are humble, today, the market for MRP software is worth over $5 billion. Understanding MRP can give you a deeper knowledge of modern inventory management and connected inventory performance solutions.
Material requirements planning (MRP) software helps manage and optimize manufacturing processes. MRP helps companies keep the minimal raw inventory needed by outputting purchase orders and other reports. MRP relies on data and requires strict data protocols to output these documents.
MRP is like the grandfather of enterprise resource planning (ERP) software, and the principles of MRP are an important part of ERP. We want to explain MRP so you can better understand how this standalone solution works for businesses such as hospitals and restaurants. We will also explain how it has informed modern solutions.
Key Takeaways
- MRP helps manage and optimize the manufacturing process.
- MRP relies on consistent and accurate data input.
- MRP is a core element of modern ERP systems.
How does MRP work?
MRP is a product-oriented approach to manufacturing and inventory control. This is why the main inputs include the master production schedule, inventory status file, and bill of materials (BOM). It’s all in support of the manufacturing process.
The two main phases of the MRP process are planning and execution. Remember that MRP software relies on consistent and accurate inputs. Businesses need to test and revise their systems to ensure accuracy.
Phase 1: Planning
The planning phase sets the foundation for the entire process. MRP doesn’t leave room for error, so documents need to meet the needs of the MRP system. For this reason, all departments need to make sure they’re using the same standards when creating:
- Bill of materials (BOM)
- Master production schedule (MPS)
- Inventory status file (ISF)
Once all the key documentation is in order, you can input it into the system. It’s important to strive for perfection, but perfection is also unlikely. With time and adjustments, the system can begin to run smoothly.
Phase 2: Execution
With key documents ingested, the MRP system can use this information to monitor the manufacturing process. In basic terms, it will look at both sets of information to determine the minimum amount of materials required. At a top level, the MRP system then determines:
- Materials required
- Amount of materials required
- When the materials are required
The MRP can then generate reports based on this information. This includes purchase orders (POs), material plans, work orders (WOs), and reports. With accurate input data, it can predict potential disruptions and provide helpful suggestions.
Why is MRP important?
MRP is important because it optimizes ordering, planning, manufacturing, and supply chain management. The MRP process focuses on your product and strives for an optimal process that reduces associated costs.
MRP is a longstanding technology that is still popular today. Additionally, it’s a key component of enterprise resource planning (ERP) and the best inventory software.
Challenges and benefits of MRP
The demands of an MRP system can lead to benefits and challenges. It can lower costs and optimize production, but this can be difficult to achieve without strict guidelines and training.
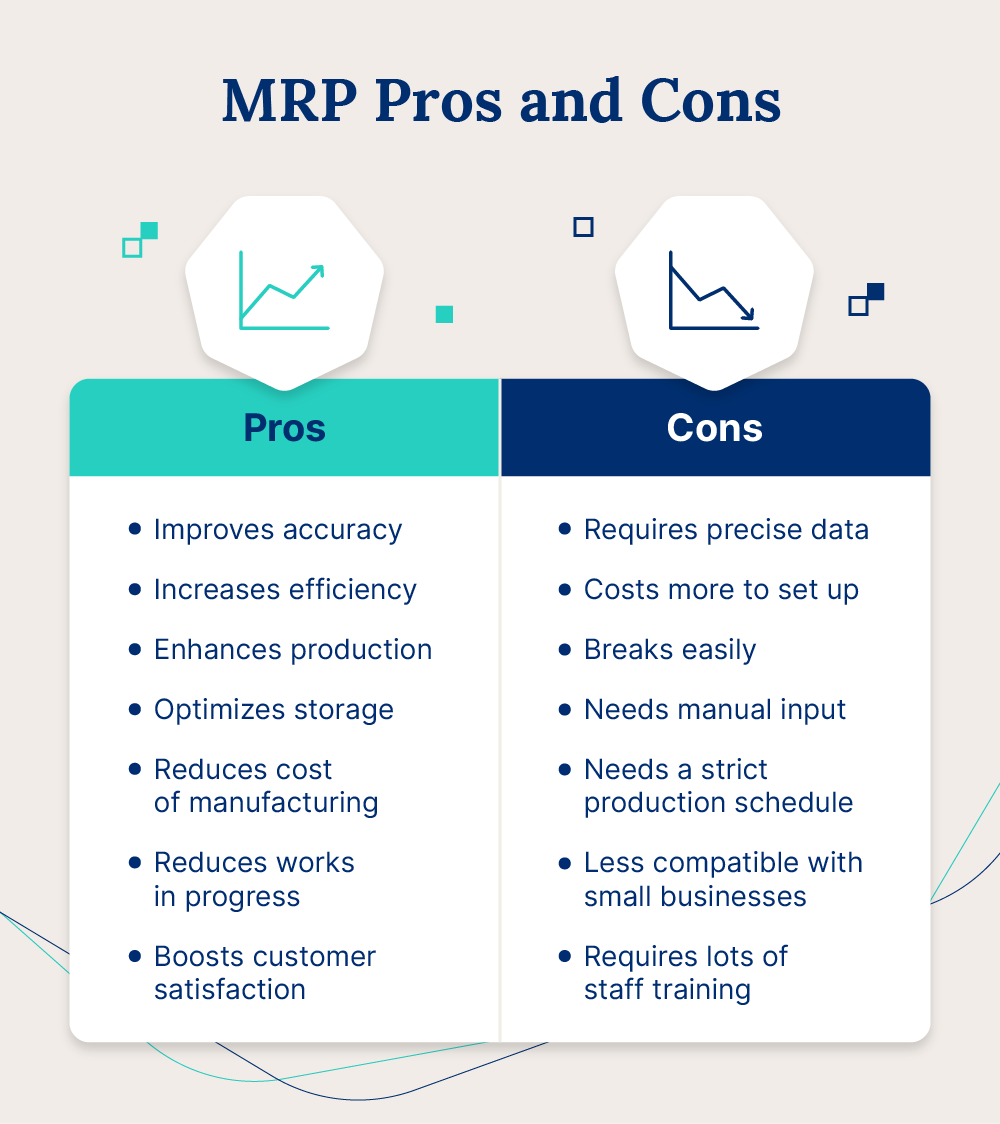
MRP inputs
MRP inputs are the key documents used by the system for analysis, monitoring, and generating outputs. Data integrity is key to a successful outcome, and all inputs need to be structured cohesively for the MRP system to understand them. To make sense of this, we will break down each of the MRP inputs.
Bill of materials (BOM)
The bill of materials (BOM) lists the materials required to manufacture a finished product. It can provide details on raw materials, components, subassemblies, consumables, and more.
The main details of a BOM include:
- Type of materials
- Quantity
- Cost
- Procurement instructions
The details included in a BOM can be extensive, including product drawings and design instructions. One of the few details excluded from a BOM is labor. However, the master production schedule will account for this.
Master production schedule (MPS)
The master production schedule (MPS) is the bedrock of the MRP process. The MPS outlines important information and timeframes concerning the production of finished products.
MPS documents include detailed information on things like:
- Deadlines
- Demand forecasting
- Alternative scheduling options
- Bill of materials
- Inventory levels
- Staffing
For a successful outcome, the MPS needs to work with the information provided in the BOM. The MPS also requires detailed information for inventory levels.
Inventory status file (ISF)
The inventory status file (ISF), or inventory status record, provides inventory information for the MRP system.
The ISF includes information on:
- Available inventory (including safety levels)
- Ordered inventory
- Procurement details (including price and lead times)
This information informs MRP outputs, the outcome of the MRP process, such as purchase orders, and other useful reports.
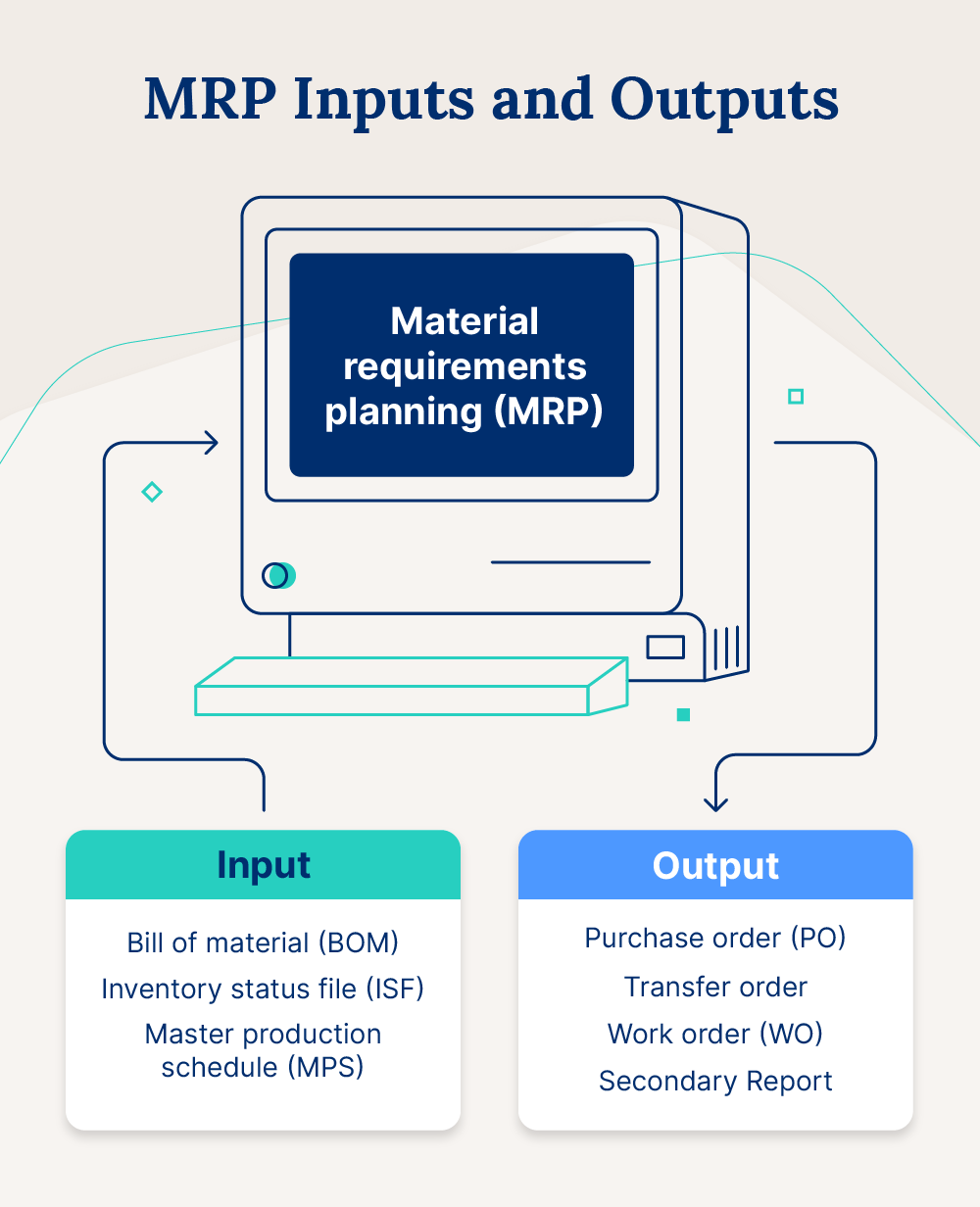
MRP outputs
MRP outputs, the manufacturing documents generated by the MRP process, rely on high-quality MRP inputs. This means the MRP outputs are only as good as the MRP inputs. With enough testing and fine-tuning, the MRP will output highly useful and detailed documents.
Purchase orders (POs)
MRPs create purchase orders (POs) based on details from the input data. The resulting POs account for time-sensitive details like purchase order lead times.
The MRP can even make suggestions for changing existing orders. This information supports an optimized production that accounts for available materials. Businesses can produce items based on demand and availability, avoiding surplus stock.
Transfer orders
Transfer orders generated by the MRP will detail the exact materials for transfer between warehouses. As with POs, these orders will make recommendations based on known time frames.
Transfer orders can provide information on:
- What to transfer
- Amount needed
- Storage area
- Destination
Work orders (WOs)
Since MRPs know what is needed and when they can generate highly optimized work orders (WOs). They can also forecast demand and make recommendations for creating the appropriate amount of stock.
Work orders can provide details on:
- Product
- Route (steps for building)
- Materials, cost, and quantity
- Labor and cost
- Machines and cost
Other reports
Aside from the main reports listed above, the MRP can output other detailed reports. These are “secondary” reports, whereas the above outputs are “primary” MRP reports.
Secondary MRP outputs address:
- Performance control: order availability and other supply chain concerns
- Planning reports: inventory forecasting and demand planning details
- Exception reports: internal issues like delayed orders and manufacturing errors
MRP vs. ERP
Enterprise resource planning (ERP) is an evolution of traditional material requirements planning (MRP). ERP software offers many solutions rather than a stand-alone solution like MRP.
MRP focuses on the manufacturing process, but ERPs can involve and inform all departments. ERPs collect information from manufacturing to marketing and beyond. The result is a broad range of modules that support day-to-day organization.
ERPs can provide:
- Workflow automation
- Real-time monitoring
- Customer relationship management
- Project management
- Inventory management
- Compliance and risk management
Beyond traditional ERP, Cloud ERP platforms offer an end-to-end solution for product-focused businesses. These advanced inventory management systems can integrate operations and finances across multiple locations. With cloud ERP technology, businesses can stay flexible with up-to-the-minute inventory information.
Who should use MRP?
MRP is best for large-scale manufacturers with predictable batch production needs. It may be less suitable for businesses manufacturing a wide range of products. Additionally, it is a production-focused tool that doesn’t provide a wide range of modules.
Small- and medium-sized businesses that sell products should consider an end-to-end cloud ERP platform. Small teams can enjoy powerful inventory management, automation, and seamless e-commerce integration.
Take your business to the next level with a free trial of Cin7’s Cloud ERP and Inventory Management.
More from the blog
View All Posts
10 best software solutions for small business management in 2024
Read More
Production Planning and Scheduling Software: What to Look for in 2025
Read More